Triton UAS entered the 2019–2020 academic year with multiple important goals to achieve, related to both administrative and technical aspects of our organization. Although at the end of the academic year we were unable to attend the annual AUVSI SUAS Competition due its cancellation in response to COVID-19, Triton UAS was still capable of accomplishing several of the goals set out at the beginning of the year.
General
One of the first goals and achievements of our year was successfully transitioning some of our members to fulfill leads positions in our subteams. We also officially established a business team to help with managing Triton UAS’ administrative tasks such as outreach, sponsorship, and finances. With the business team operational, the other subteams could focus on their respective technical goals related to the project.
Another big focus coming into this year was the recruiting, retaining, and training of our members. For recruitment, we presented to many of the introductory engineering courses and a SWE general body meeting. We also tabled at the fall and winter Engineers on the Green events. For retention, we focused on giving our members interesting and impactful projects even if they had little experience. We used these experiences as opportunities to train our members in the tools and engineering concepts they need in order to accomplish their goals. Additionally, at the beginning of the year, we teamed up with the UCSD Envision Maker Space to hold a Solidworks workshop and also held our own composite layup workshop to give our new members the basic skills they need. This year had been one of our most successful years in retention and training until COVID-19 forced everything to be virtual. We hope that many of them will return next year, and that we can replicate our success next year as well.
We have also been very successful this year in maintaining an active outreach effort with other UC San Diego organizations and local high school, High Tech High Chula Vista. Triton UAS was involved in multiple UC San Diego outreach events this year, including the SWE Envision 2020 Project Fair, Corporate Affiliates Program Tabling, and Virtual Triton Day. In collaboration with High Tech High Chula Vista, a few of our subteam leads had opportunities to share to with students more information about Triton UAS and provide insight on the students’ own aerial projects. More information about our outreaching and the events we attended can be found on our blog under the Outreach tag.
In addition to Professor Ryan Kastner, Triton UAS has a new co-advisor, Professor John Hwang from the Mechanical and Aerospace Engineering department. Professor Hwang works on multidisciplinary design optimization, aircraft design, satellite design, aerodynamic shape optimization, structural optimization, and trajectory optimization.
Lastly, although we were unable to attend the AUVSI SUAS Competition, we were still able to complete and publish our Technical Design Paper prior to the planned competition deadline.
Airframe Team
Swallow
Coming into the year, we had a pre-purchased Swallow airframe that was bought due to the competition’s new payload capacity requirements. However, the unmodified airframe was not suitable for the added weight and thrust requirements. This year, we were able to implement a power system, change out many of the fasteners, design and manufacture mounts for electronics, add motor mount reinforcement, add landing gear reinforcement, and even redesign and manufacture the vertical stabilizer to allow for steering during takeoffs and landings. We were also able to design a lightweight adaption piece to allow us to use our current gimbal design on the Swallow. With the Swallow, we were able to have many successful flights. Our goal now is to modify the Swallow to allow it to carry and drop the unmanned ground vehicle, test and finalize the gimbal adaption piece, and tune the PID controller until the plane is fully autonomous.
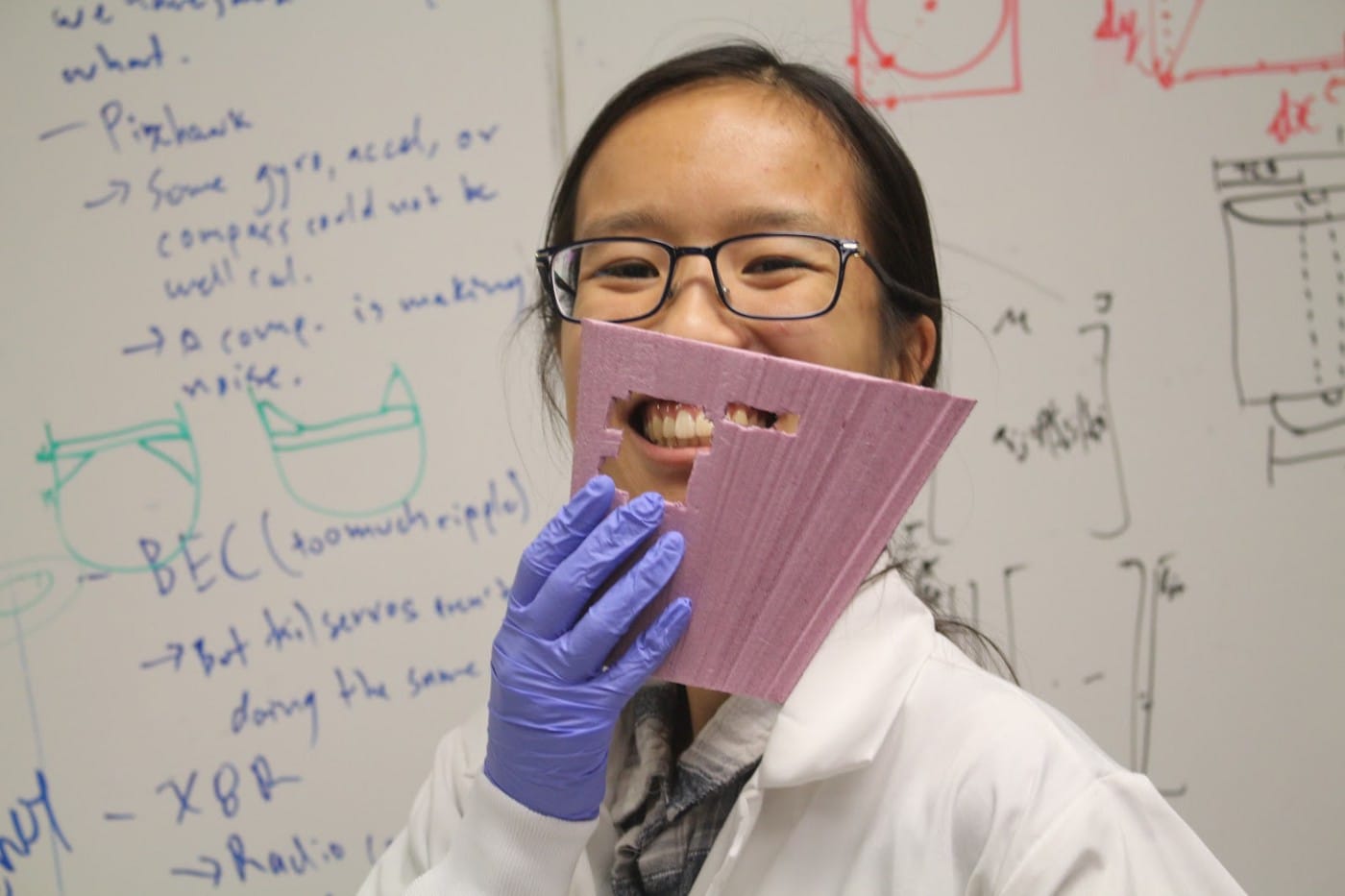
Additional Airframes
After the success of the first Swallow, we decided to purchase a second Swallow to serve as our backup airframe. Beyond renaming it, our goal next year is to use our experience from outfitting the first Swallow to quickly outfit the second so that we can tune it before the competition.
The Swallow replaced the Fiber One as our main flight platform. However, we still made it our goal to start rebuilding the Fiber One to serve as another backup airframe, and to train our members in composite manufacturing. This year, we manufactured the horizontal and vertical stabilizers, prepared all of the outer wing sections for layup, and tested a new manufacturing procedure for the tail boom. Next year, we plan to continue manufacturing, and finish the Fiber One before the end of winter quarter.
A trainer airframe was assembled and outfitted this year to train new pilots on the tuning and operating of similar onboard equipment that are used in our competition airframes. It was also repaired after a minor accident that damaged the cowling and parts of the wing structure and skin. Overall, this trainer had multiple successful training flights under the control of our new pilot that gave him the necessary knowledge and experience. However, the trainer airframe was ultimately destroyed in a crash when the flight controller malfunctioned during a training flight. We plan on outfitting another existing trainer airframe next year to continue training our new pilots.
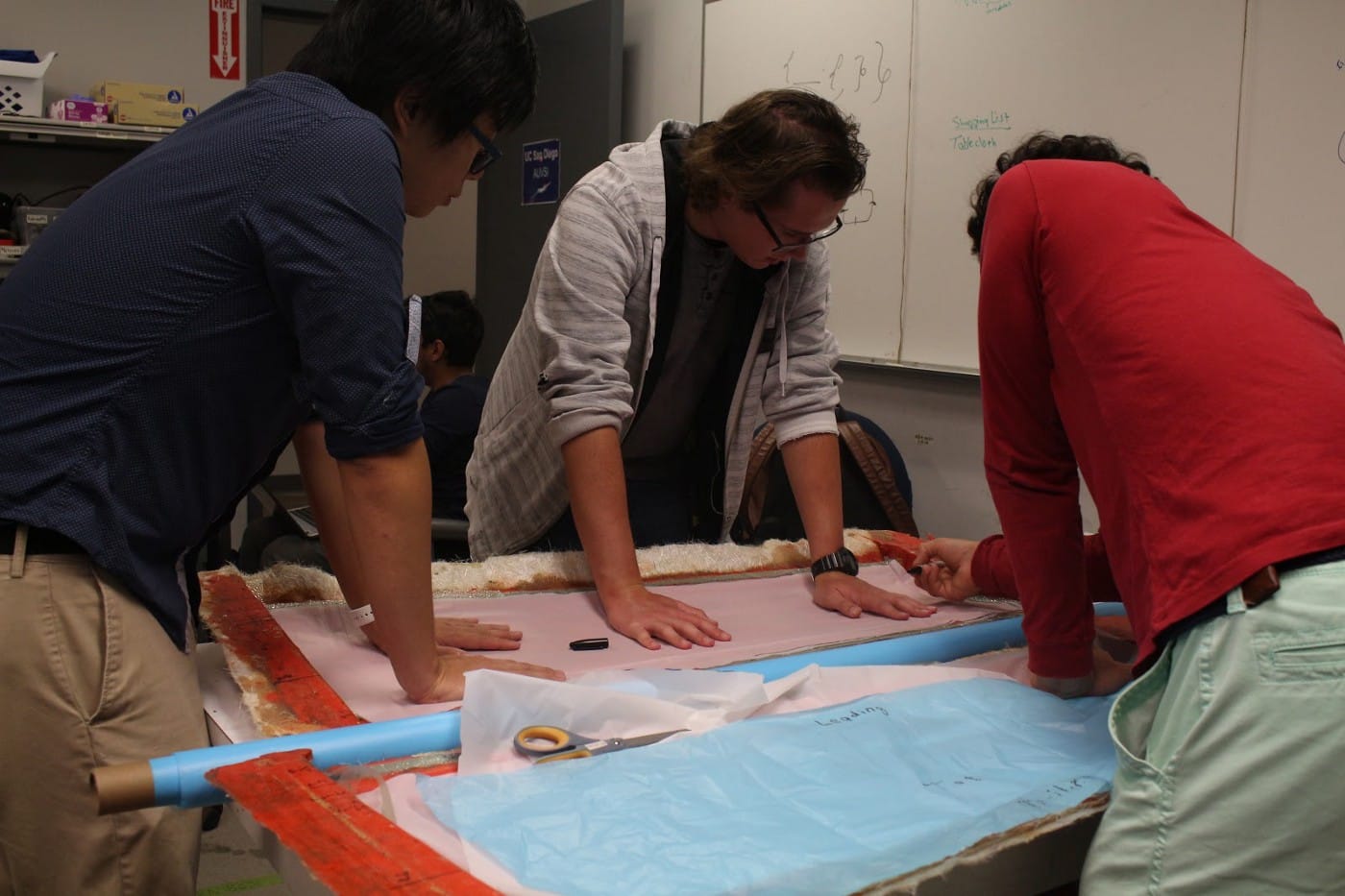
Unmanned Ground Vehicle (UGV)
Last year, the UGV project ran into issues with the electronics, so this year the embedded subteam was consulted to get a full understanding of the system and electronics required. Over the course of this year, custom mounting of these electronics were integrated into the design of the custom chassis and were successfully 3D printed. Additionally, custom wheels were designed and 3D printed using a flexible rubber filament for better impact behaviour. With the chassis almost complete, the UGV team, now a team with members from the airframe, embedded, and software subteams, will turn its attention to designing a custom PID controller for the UGV to allow for autonomous control of a parachute, and autonomous driving to achieve the mission tasks.
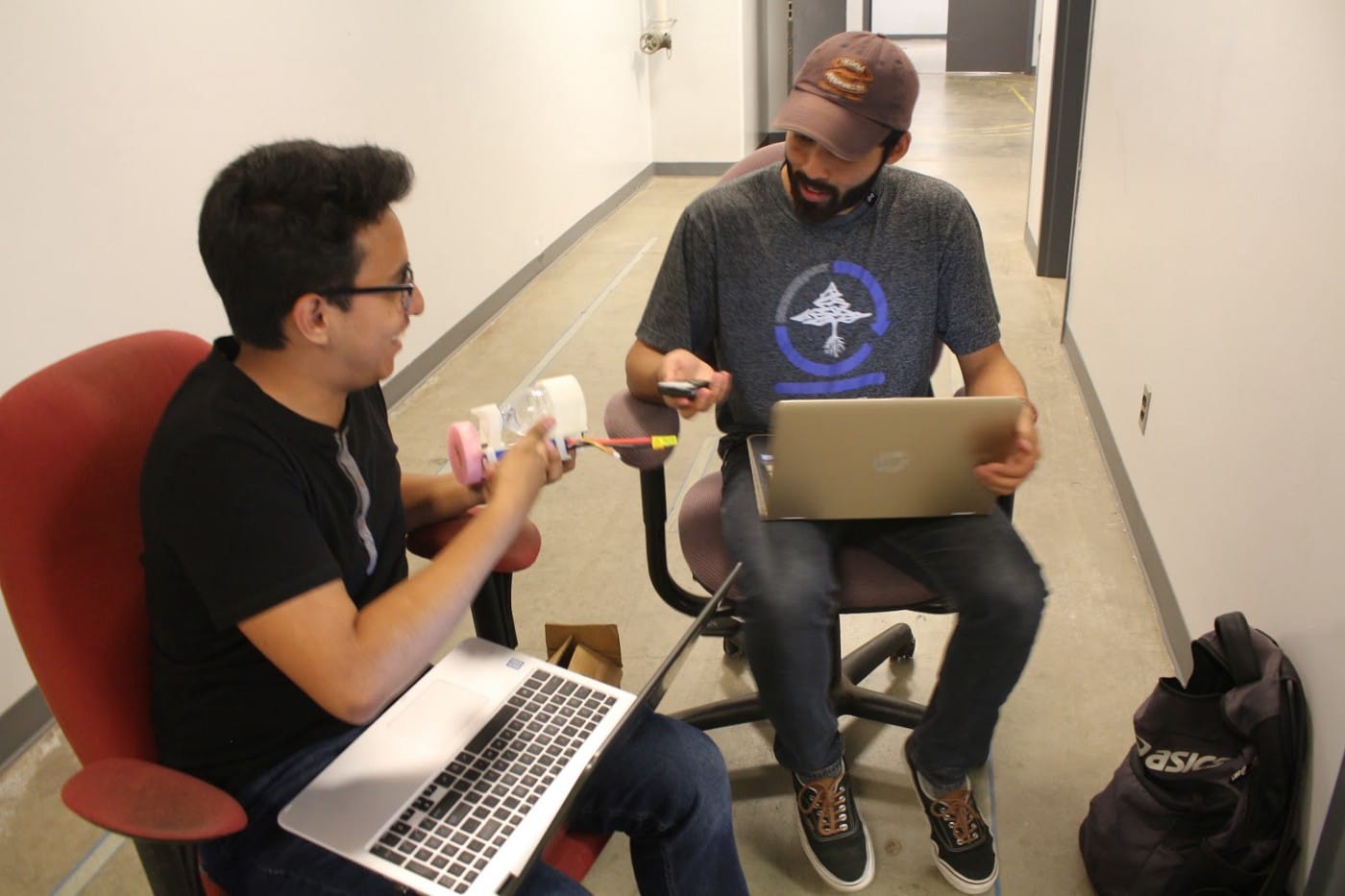
New Plane Design
Due to the evolving rules of the competition and the increased payload requirements, we decided that we wanted to design a new plane. This year, we researched and developed a model to calculate the aircraft performance based on a series of design variables. This model was then used to create a simple aircraft design optimization program in Matlab. We have also started consulting with Professor Hwang on how to use the aircraft design optimization software that he uses in his lab, OpenMDAO. Additionally, we started familiarizing ourselves with analysis tools such as XFoil, Ansys, and AVL in order to validate and characterize the performance of potential designs. Additionally, we evaluated the pros and cons of different airframe configurations and have narrowed it down to either a conventional or flying wing body design. Our goals for next year include finalizing the design, creating the design in Solidworks, creating the molds, manufacturing and outfitting the airframe, and tuning the plane before competition next year.
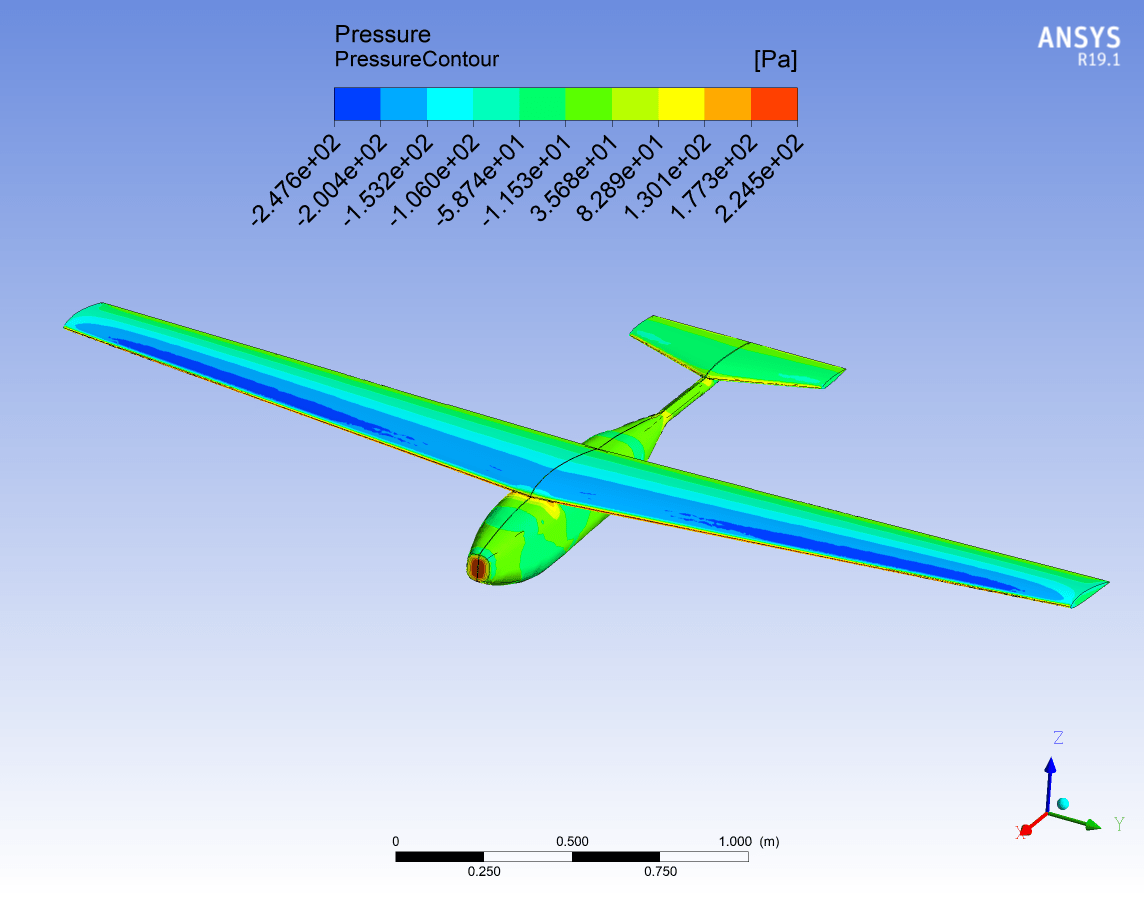
Embedded Team
Power and Signals Board
This year, the embedded team split the power distribution from previous years into separate boards, i.e. power and signals. This decision aims to solve the complexity of previous designs and prevent total failure in the case of a specific malfunction in the electronic systems. The team has selected components for both boards at this point, and it is working to test out the limitations of each design. Due to stay at home orders, the team has to come up with ways to keep these projects going forward through the use of simulation software.
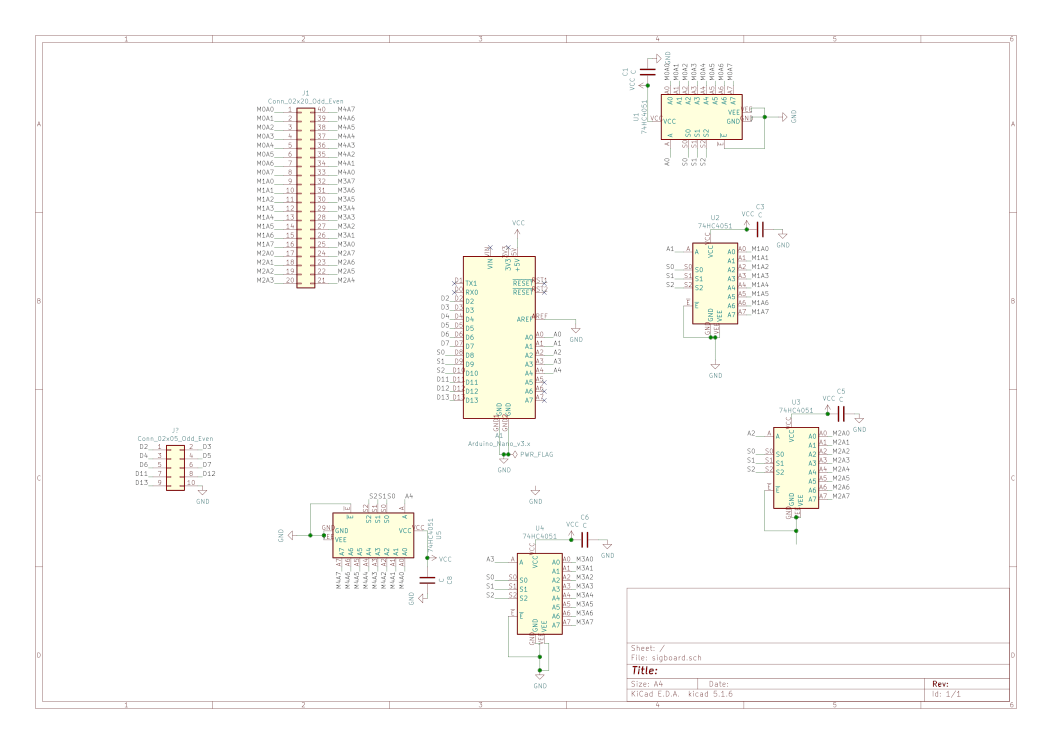
Antenna Tracker
Additionally, due to several issues and a lack of features in last year’s antenna tracker software, the embedded team took upon designing and implementing its own antenna tracker software. At the moment, the antenna tracker software has several scripts that are in the testing phase to consolidate the serial communication across different devices, i.e. ground control station computer and microcontroller. Unfortunately, the team has not had access to the lab, and this task has landed on one person as access to the components necessary is scarce. However, the team expects to see positive results for this project after this testing period.
UGV
The embedded team has been working closely with the airframe team and the software team this past quarter to push forward the unmanned ground vehicle design. This project is at a stage where there are many tasks that members can work on while at home, so the team has invested a significant amount of time researching and conceptualising comprehensive designs for the dropping mechanism. Specifically, the embedded team has analysed all the possibilities for controlling software, and the team is currently working in a mathematical model for the dropping mechanism to design a new controller that is more versatile.
Test Flights
Furthermore, with the help of the airframe team, the embedded team successfully set up the electronic devices that are required for the Swallow. While there were less test flights this year, the embedded team was able to assist in completing tuning STABILIZE and FWA (Fly-by-wire A) modes for the Swallow. The team expects to finalize tuning for all modes of the Swallow by the end of next Fall Quarter. Additionally, the team has started to take steps to consolidate materials for setting up other planes, such as a trainer plane and backup planes.
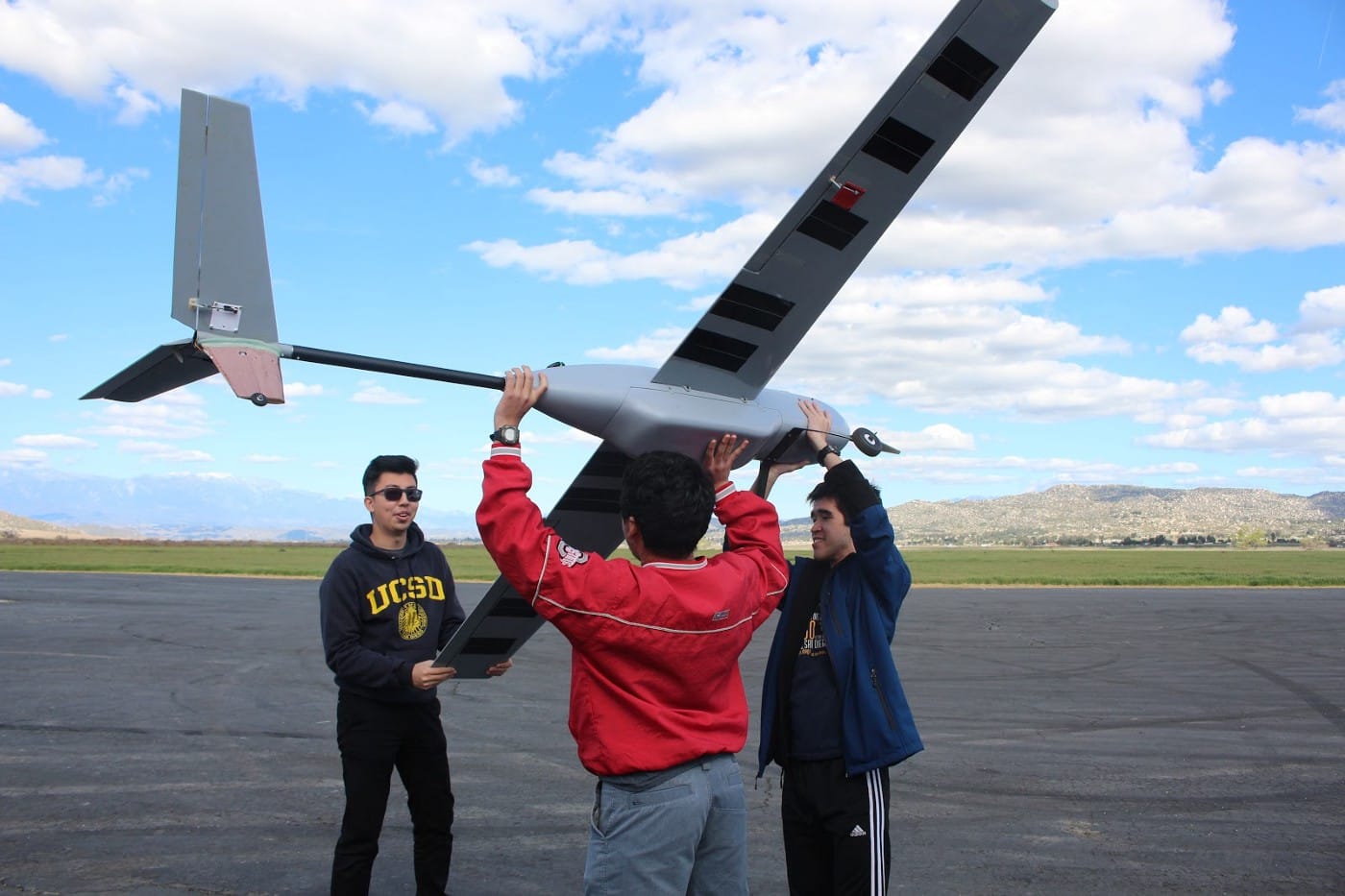
Software Team
Computer Vision
Many new members were interested in working with computer vision, so a large focus for the year was teaching the newcomers tools like Python, OpenCV, Pytorch, and computer vision algorithms like concave hull segmentation and K-NN classifiers. We also use a variety of modern deep learning algorithms, such as transfer learning with Faster R-CNN for object localization and convolutional nets for letter and shape classification. Our image segmentation code was refactored to improve efficiency and accuracy. One downfall with deep learning is it requires large amounts of well labeled data, which we simply could not collect ourselves. To solve this, we created a tool to automatically generate artificial targets. These datasets have more variety than we would be able to capture at our test flight field, and we can improve their quality over time through code instead of by capturing new images.
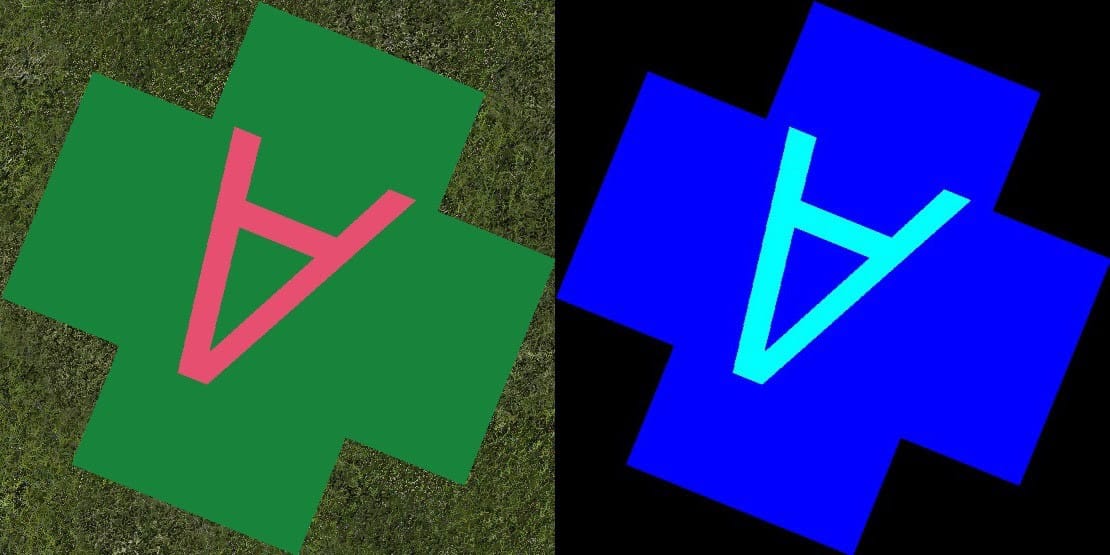
Path Planning
This year the AUVSI competition upgraded the moving obstacle challenge by making the moving obstacle another teams UAV. In order to complete this challenge the software team made significant upgrades to the way that paths are created and visualized, allowing for better analysis of performance and efficiency. The path visualization software went through many iterations and improvements over the year, resulting in a product that allows for insightful analysis of path generation, obstacle avoidance, and search area coverage. Many bugs in the Dubins curves path generation algorithm were ironed out and it has now reached the state where it can be deployed for actual missions. Although our path planning system is operational, there are still many improvements that we plan on making that will make it even more robust and efficient.
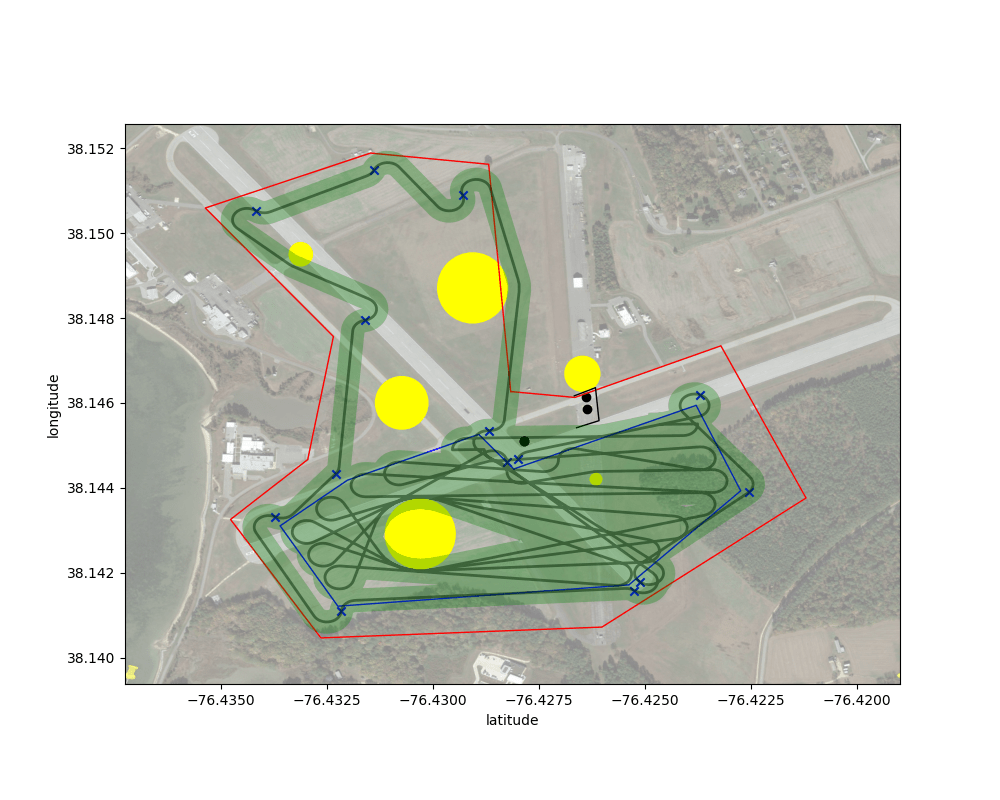
Business Team
The 2019–2020 year marked the official inception of the Triton UAS’ Business Team, with goals and objectives centered around maintaining the organization’s public relations, corporate outreach, financial accounting, marketing, and other administrative assignments. By establishing a separate subteam to manage and upkeep these functions, the other subteams in Triton UAS are free to focus solely on their respective components of the organization and technical duties related to the aircraft.
This year, the business team was devoted to providing detailed updates on what the organization has been working on each quarter and about any outreach that Triton UAS has been involved in. Through these updates the team hopes that sponsors, members, and other interested parties have a thorough depiction of what are Triton UAS’ concrete goals and what steps are taken in pursuit of these goals. Furthermore, this year the business team has been active in researching new avenues for securing the required funding for our project and attendance to the AUVSI SUAS Competition, though it was unfortunately cancelled this year. Despite this fallback, Triton UAS and the business team were still able to garner and appreciate the support provided by the UC San Diego Data Science Institute, Mechanical and Aerospace Engineering Department, and the Electrical and Computer Engineering Department. Additionally, the business team has taken steps to update the Triton UAS website, brochure, and promotional materials in anticipation of pursuing new possible sponsorship opportunities in the coming year.
Despite the circumstances in the later parts of the 2019–2020 year, Triton UAS has managed to learn and achieve a great deal due to a yearlong unified effort amongst our subteams and its members. Whatever the challenges may be in the next academic year, Triton UAS is committed to achieving our goals and fostering an environment for all of our members to learn and grow in.