Triton UAS’ Winter Quarter was filled with significant milestones for both our project and outreach efforts, such as the maiden flight and tuning of our main flight platform, the Swallow, and various outreach events throughout the quarter.
Triton UAS was involved in several outreach opportunities with the local and UC San Diego community. The quarter started with new member recruitment at the Winter Engineers on the Green. This was the first opportunity of the quarter to recruit fellow students to our project. Triton UAS continued outreach efforts with a presentation to the students at High Tech High Chula Vista about our organization and project. Leads Andrew Fletcher and José Orozco explained how we develop our year-long project and answered questions about us, our project, and UC San Diego. We also participated in the SWE Envision Project Fair, where we tabled alongside other UC San Diego project organizations and introduced our project to visiting high school girls from the San Diego area.
Due to the precautions taken by UC San Diego in response to the recent coronavirus pandemic, the university has temporarily suspended non-essential gatherings on campus. With these precautions in place, many outreach events have moved to an all-virtual platform. Triton UAS has also adopted virtual methods to continue project operations and outreach. For Virtual Triton Day, Triton UAS produced a video for the Structural Department’s Virtual Triton Day YouTube playlist introducing students to our organization and the learning opportunities our members have with a hands-on project. For the Overnight Engineering Project Fair, Triton UAS contributed to creating a slideshow (Slide 22) about our organization that will be presented to students digitally for them to see what the university has to offer.
Triton UAS has made significant progress on the project as well this quarter. With our main airframe, the Swallow, ready for flight, we conducted three test flights to tune the plane. Additionally, we have been in the process of transitioning our current airframe lead, Andrew Fletcher, into the project manager position as our current project manager, Jessica Chan, is set to graduate this June. As such, recently Andrew has been leading the subteam leads meetings and engaging in the business subteam meetings. Due to coronavirus and social distancing orders, all current and future meetings this academic year will be conducted through an online format.
Unfortunately due to the coronavirus pandemic, the AUVSI SUAS Competition was canceled this year. Despite this, we will still be writing and publishing our technical design paper by the original competition deadline, May 15th. Depending on news about the California shelter in place mandate, we will also produce a flight readiness review video and host a mock mission demonstration with deadlines adjusted according to our ability to have test flights. The rationale for this is that this will allow us to prepare for next year’s competition, show potential and current members, future and current sponsors, as well as UCSD engineering departments what we have accomplished this year despite these limiting circumstances. We will still be having online meetings for subteams which will be updated on our calendar.
Airframe Team
Swallow
We finished outfitting the swallow with the necessary electronics, custom mounts, and reinforcements that it needed. During Week 6, we held our maiden flight for the Swallow. It was a successful maiden flight for the Swallow, however it wasn’t all clear skies ahead. As the swallow landed after it’s first flight, there was some unanticipated crushing in the landing gear area. After a short investigation we diagnosed that the structure in the area was not satisfactory for the payload we were carrying in the plane. After consulting Professor Hyonny Kim of the UCSD Structural Engineering Department, we reinforced the landing gear area, and since then, have seen no further damage, even after numerous flights and landings. Then, all was well until the Swallow’s vertical portion of its Y-tail and attached tail wheel broke off on landing. We determined that the root cause was because the tail wheel on the Swallow did not have any steering. In response, we were able to design and manufacture a completely new steerable vertical stabilizer and tail wheel from scratch before the next scheduled test flight. After more successful flights and tuning, we gained confidence in the Swallow as a platform and purchased a second one as a backup. We also started working on and made considerable progress towards adapting our camera gimbal design for the Swallow, and making a case to protect the PID controller on the gimbal.
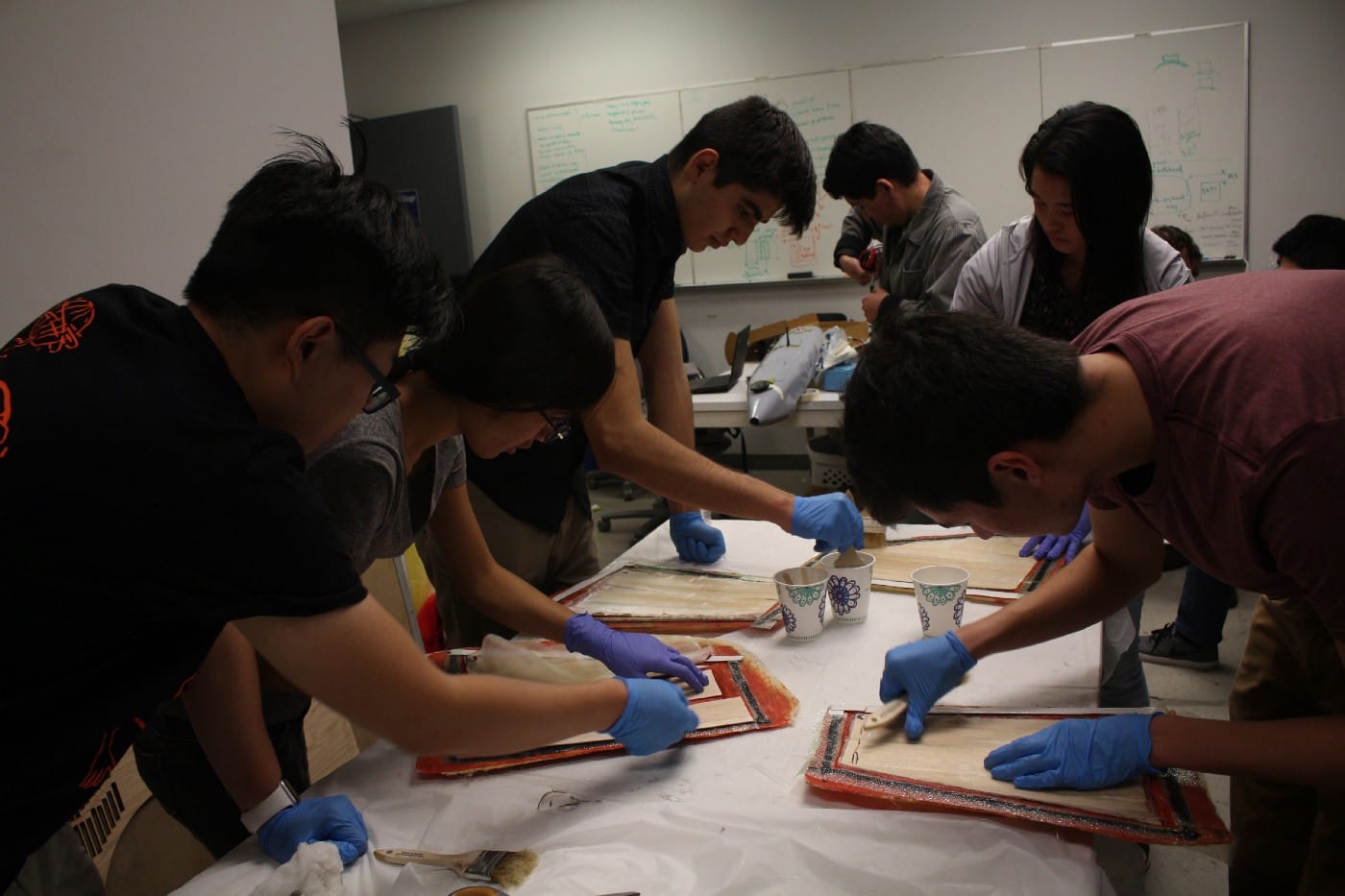
Fiber One
Our focus this quarter was to prepare and maintain the Swallow for flight, but that didn’t stop us from making progress on the Fiber One. We were able to prepare and complete all six of the wet layups for the tail pieces. Additionally, we have fully prepared materials for all four layups for the outer wing sections.
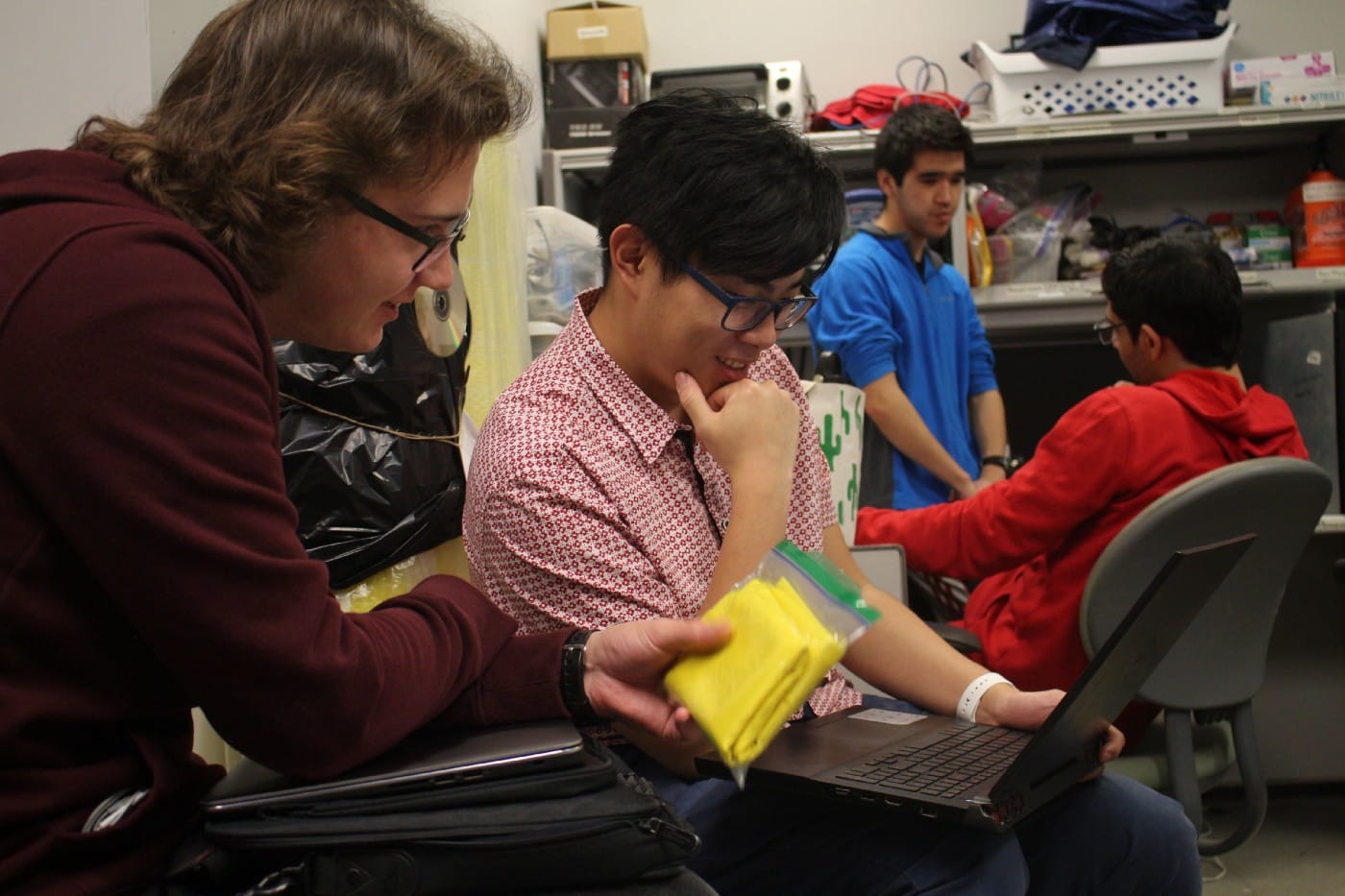
Unmanned Ground Vehicle (UGV)
We made progress on the UGV in every aspect. For the chassis, custom, secure mounting was added for all the electronics and the smaller battery, and the chassis design was validated by 3D printing a prototype and testing the mounts. For the electronics, we decided to switch to a Cube Mini since we didn’t need many of the extra sensors, and could benefit with size, weight, and cost savings. For the dropping mechanism, we proposed and started working toward a new design. This design includes two separate mechanisms: a spring loaded hatch to maintain the aerodynamic properties of the fuselage, and a servo release mechanism that is designed to securely hold the UGV in place through the rigours of flight, and perform a controlled release at the desired instant. Additionally, we finalized the design of the parachute, and started researching ideas for releasing the parachute. For the wheels, we designed and tested many different ideas that included wheels that were completely PLA, a mix of PLA and NinjaFlex (a flexible 3D printing filament), and completely NinjaFlex. After extensive prototyping and testing, we settled on the completely NinjaFlex wheels due to their strength and ability to absorb impacts. We finalized the design by adding space for a collar on the short motor shaft, and anticipate using this as our final wheel design going forward.

Version Control
Since we have a team of ten active airframe members, many of our members will work on the same projects in parallel. This has created a large number of files that need to be organized. For this reason, we decided to switch our version control from Google Drive to Github. While it took a little bit of time for us to learn how to use Github, we will benefit in the future with better organization and a new, useful skill.
New Plane Design
In working toward our new plane design, much of this quarter was spent on research, and learning software tools to aid in the process. We researched topics such as calculating the Oswald efficiency factor by reading a combination of research papers, educational websites, and other online resources. Also, our leads continued learning how to use tools such as XFoil and Ansys, and our members continued to practice their skills in Solidworks.
For our first Swallow, our current and final goals are to install the UGV and camera gimbal such that we can attempt those portions of the competition. Once this is done, the Swallow airframe will be ready for a full mission. Also, using our experience from outfitting the first Swallow, we plan on outfitting and reinforcing the second Swallow quickly to serve as our backup airframe. For the UGV, the plan is to have a fully functioning UGV with confidence that it can reliably complete its entire mission. To do this, we need to finalize the chassis design and perform many drive tests and drop tests. In addition to all these goals, our main focus will be shifting toward a new plane design for future years. This will include training our team on how to use tools such as Ansys, XFoil, AVL, xflr5, and XROTOR, in addition to continuing to gain experience in SOLIDWORKS and MATLAB. The end goal is that, with the help of these tools, we will finish the preliminary design of the plane design by the end of the quarter.
Embedded Team
Power Board
The team has selected the components for prototyping the power board, and aims to have a working prototype by the end of the next quarter to use on test flights. Additionally, we will test that our power system design will be as efficient as possible, as our 4S Li-Po payload battery limits how much power we have available. Hence, we will work closely with the software team to come up with various scenarios that can simulate the power draw of the electronic devices while tasks are performed during missions. Furthermore, we aim to implement a kill switch for all non-flight critical electronic devices in case we reach low power during a mission, to ensure the Swallow lands safely.
Signals Board
Similarly, the team has selected the components for prototyping the signals board, and also aims to have a working prototype by the end of next quarter to use on test flights. Furthermore, the new signals system will have enhanced capability to measure large numbers of analog data streams, to improve logging data that can be used for future design revisions of other systems. Further, the signals system will be on a separate board from the power system, to allow for independent revisions to each system, simplifying both the development of each, and the process of adapting to changing power or signals requirements with new designs.
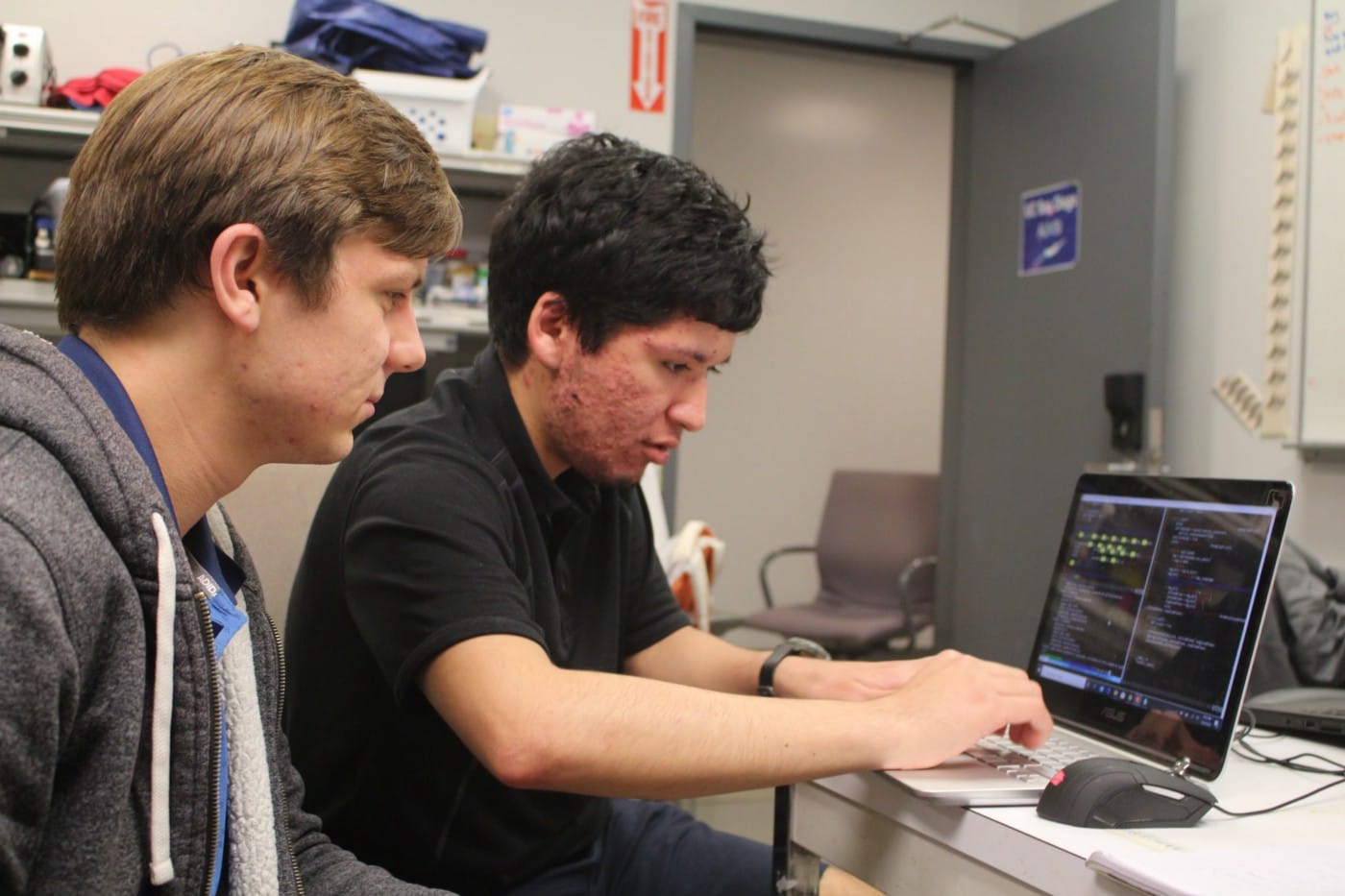
Antenna Tracker
The team also successfully developed a virtual prototype. To avoid spending a considerable amount of time on the script for parsing MAVLink messages, we opted for using Python to implement both the MAVLink parser and the mathematical models to obtain the pointing direction for the antenna tracker, as the MAVLink Python libraries seemed simpler for our use case. Hence, currently we are implementing the connection between these Python scripts and the Arduino script that will command the servos to move to a given angle. Additionally, we are working on adding a GPS module to the antenna tracker. This module will automatically acquire the geoposition of the ground control station for the Python scripts to use in the process of calculating the pointing direction.
LiDAR Research
In addition, the team began researching LiDAR modules for detecting dynamic objects which was a new task added to the competition this year. The team has come up with various options, but we are still analysing how we could implement them, since these modules would be prone to damage, and even modules at hundreds of dollars can be out of our budget due to the need of replacing them. Additionally, we have noticed that many cheaper modules do not necessarily use laser modules, but infrared modules. Hence, we are comparing how each works to know if using infrared could affect our use case. Currently, we do not expect to install a LiDAR module on the Swallow by the end of this year, since this would translate to many changes to our current platform, but we expect to come up with a solution for next year.
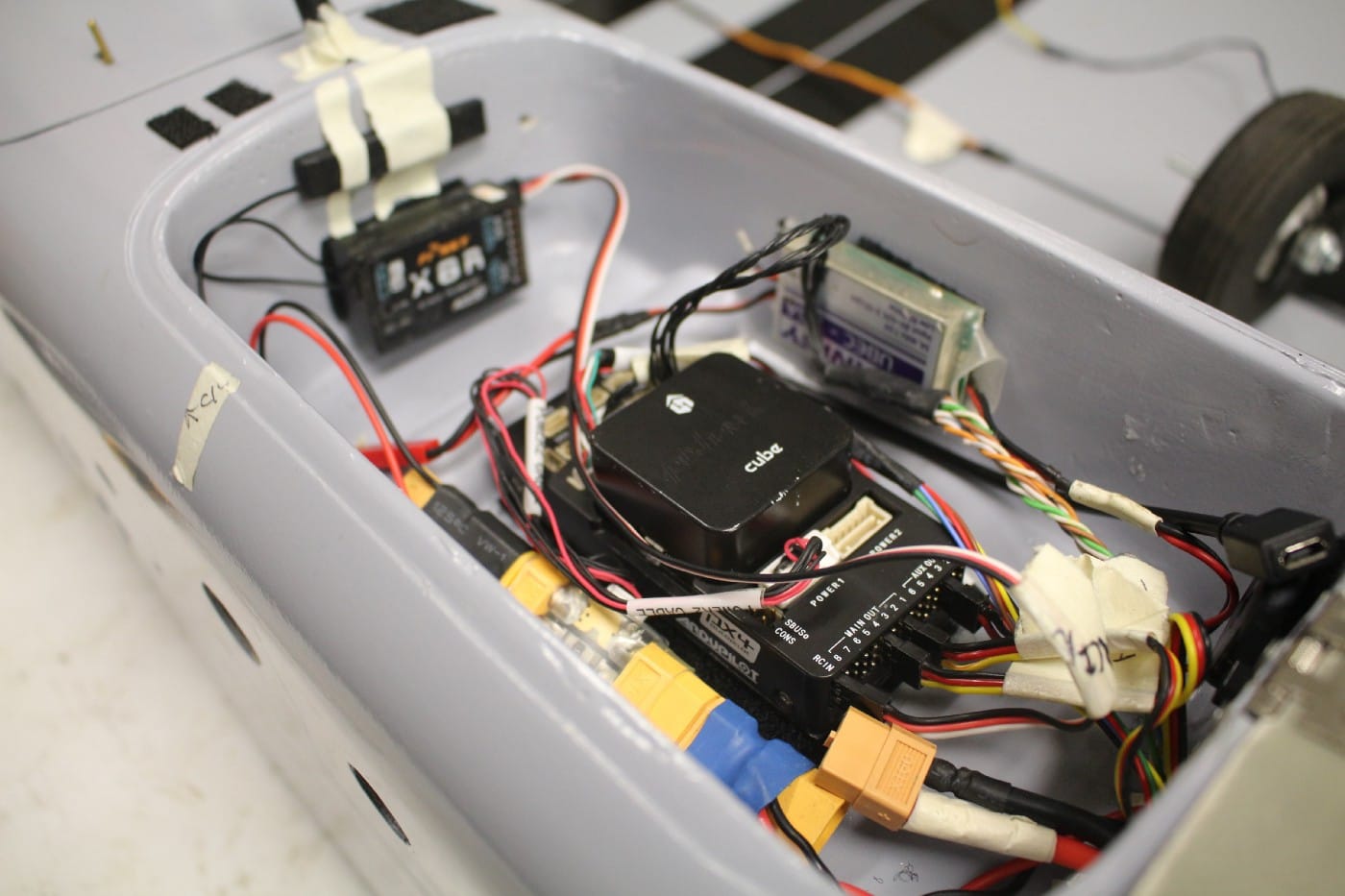
Swallow
Moreover, with the help of the airframe team, the embedded team successfully set up the electronic devices necessary for us to start tuning the Swallow. However, during this process of setup, the team did face some problems with electromagnetic interference. Thus, we rearranged the various components inside the Swallow to set most EM devices perpendicular to each other. In addition, after the Swallow suffered some damage on its tail at landing, we assisted the airframe team to connect and set up the new ground steering for the Swallow.
Software Team
Computer Vision
After realizing the limitations of an open-source target generator that we were testing, we decided to build our own generator that can be used to create custom training images for saliency. We completed the networking for the computer vision suite by utilizing the master-agent design pattern and connecting the different nodes using the ZMQ protocol.The team also had tremendous progress on the individual components of the CV mission task. Segmentation was updated to decrease redundancy while increasing efficiency and performance. The design of saliency was reengineered to use the PyTorch implementation of FasterRCNN instead of a spectral saliency algorithm. Classification of alphanumeric characters was also completed by implementing a neural network trained on binary masks. We also gained new members this quarter that were very interested in learning more about the fundamentals of machine learning, so we began the process of building our own network to classify shape.
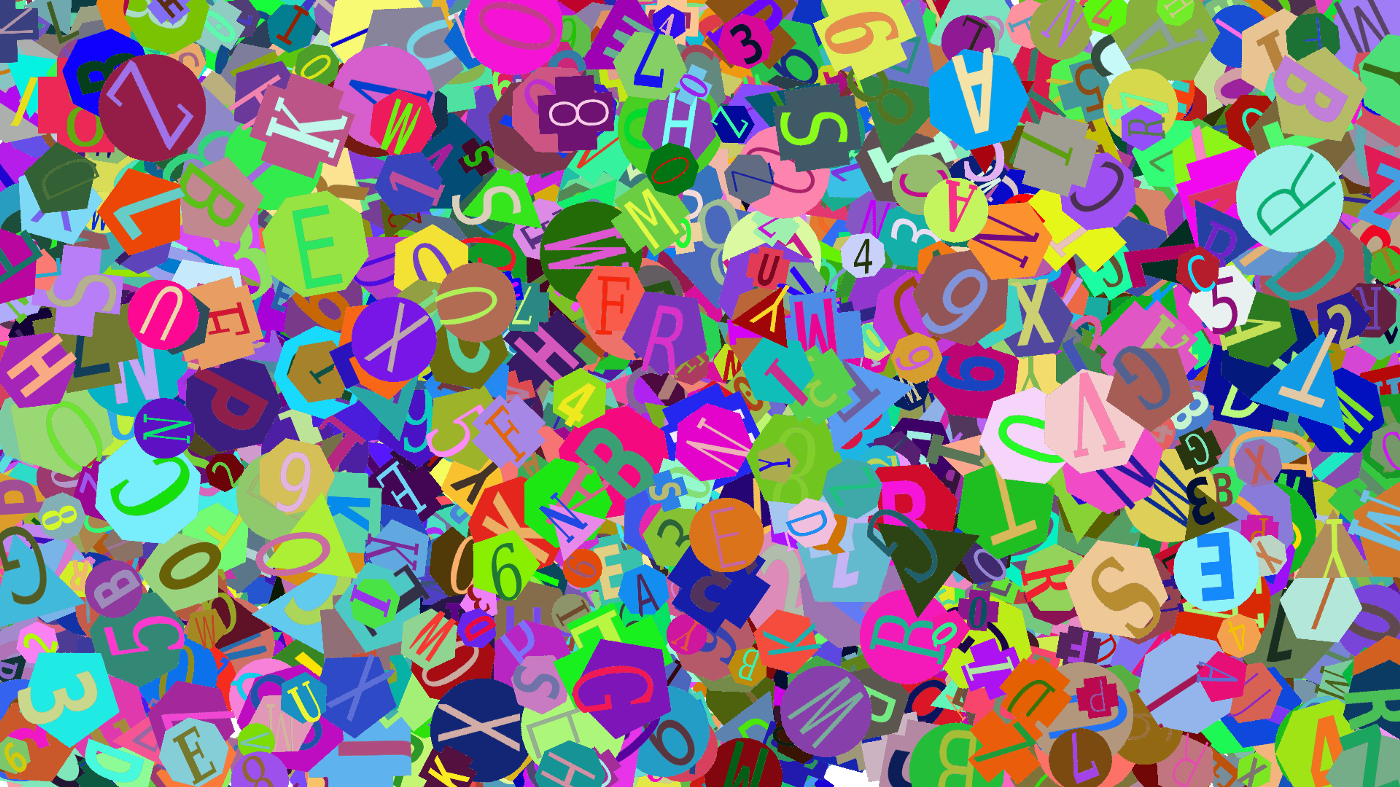
Path Planning
Most of the progress this quarter has just been debugging the current implementation. We fixed a bug where the path would randomly jut out in the wrong direction. Since the competition rules changed so that the search area of target classification is now the same as the entire fly zone, we also encountered a bug where the generated path would exceed the flight boundaries. This was also fixed. We had two new members that joined that were interested in learning more about the inner working of the Dubins algorithm we implement, so they began the process of refactoring the code base to be more mathematically sound.
Now that we have working components for computer vision, our main goal is to integrate them all together and acquire some concrete benchmarks for the performance of both the individual nodes and the system as a whole. We will continue to experiment with different neural network frameworks and architectures to improve saliency and classification. The end goal is to actually submit our targets to the judging server, so we also will integrate our CV suite with the judging server, thus completing the CV task. In order to get it to work, we have to determine the best way to split up the search area to produce the most efficient path. Dynamic obstacle avoidance is also a crucial component that needs to be added to the system. To accomplish this, we will have to add an additional module that can upload intermediate waypoints to the Pixhawk while it is already in the air.
Business Team
The business subteam this Winter Quarter has been devoted to maintaining a consistent line of communication through blog posts and updates on our Medium. With regular blogs, both our members and supporters are able to stay up-to-date with any progress and information about our project.
Additionally, our team was previously occupied with raising funds for this year’s AUVSI SUAS Competition. Due to the dates of competition falling outside our academic year, Triton UAS was not able to get the normal amount of competition funding that is provided by on-campus funding sources. As such, Triton UAS had to raise funds through donation pledges made by departments of the university. Thanks to the UC San Diego Data Science Institute, Mechanical and Aerospace Engineering Department, as well as the Electrical and Computer Engineering Department, we were able to raise over $7000 in donations within just two weeks. Although the competition has unfortunately been cancelled this year and the pledged donations were not utilized, it was not in vain because of the experience gained from communicating directly with the departments and sharing our mission as an organization.
Going into the next quarter, the business subteam intends to keep bringing consistent and clear updates with ongoing project developments and organization plans moving forward. The team will also be working on updating the team’s brochure, website, and other promotional materials in preparation for contacting new companies about possible sponsorships.
The Spring Quarter for Triton UAS will look a little different in our day-to-day operations, but the vision and plans for our project remains the same as it has in our previous quarters. Our subteams will work hard to see their goals come to fruition, and we will be sure to provide updates on our progress.