After 2018 competition in the spring, the software, embedded, and airframe subteams have been hard at work improving upon our experience from the 2017–2018 school year. Here’s an update from each of our teams:
Software
With the removal of moving obstacles from this year’s competition rules, the software team can now reallocate energy to mission tasks such as object detection, localization, and classification as well as stationary obstacle avoidance.
For computer vision tasks, we are working on implementing and training different machine learning models to determine the model with the highest accuracy. Some of the models we are implementing are Mask R-CNN and YOLOv3 to crop images around the targets. To train and test our models, we are making and taking aerial images of our own targets to collect data, and holding data labeling meetings for use of the data with the models.
For path planning tasks, we have combined our different visualization and testing tools into a single cohesive user interface so that we can easily understand the performance of our algorithms. Further plans include integrating this GUI with the Ardupilot SITL (software in the loop) plane to automatically run the simulated plane through our paths so that we can understand how well the plane can fly our different paths.
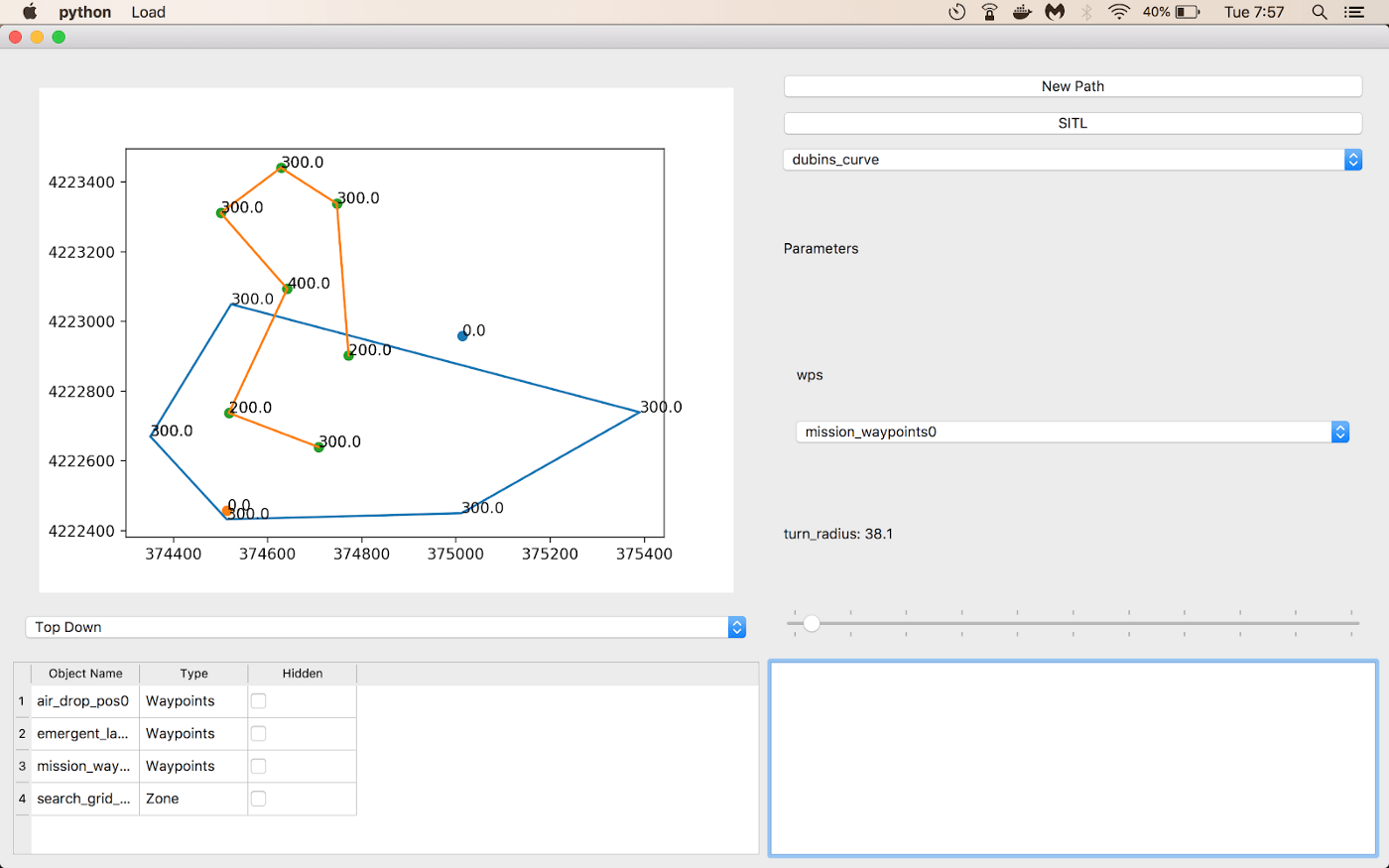
Embedded
The embedded team has focused on recruiting and retaining new members by splitting people off into multiple meetings, allowing us to give more attention to each member. So far, we have finished soldering a duplicate of a PCB (printed circuit board) that powers devices on the plane, and set up new recruits to design a new revision of the PCB to fix previous issues with the board. We are also developing an antenna tracker that will automatically point a WiFi antenna and track our plane during flight.
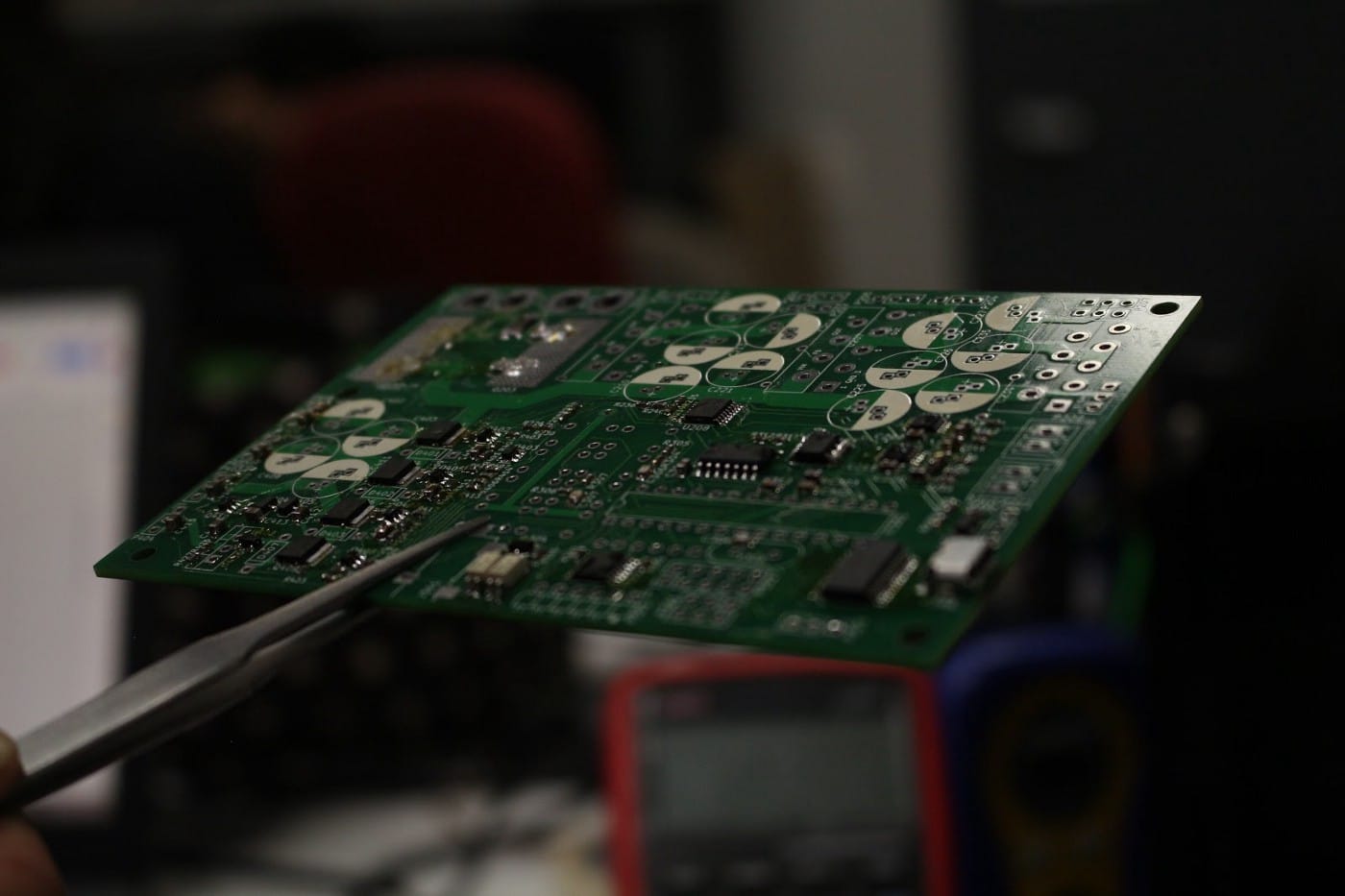
This year we have moved on to the Pixhawk 2 as the flight controller for our main flight platform. Previously, the Pixhawk 1 suffered from sensitivity to vibrations during flight because the IMUs (inertial measurement units) were firmly attached to the board. The IMUs in the Cube are dampened with foam to reduce sensitivity to vibrations. Additionally, the Cube contains multiple IMUs for redundancy and can be powered from two redundant power sources, making it the ideal flight controller in terms of reliability. We will still continue to use the Pixhawk 1 for developmental platforms due to its lower price point such as the unmanned ground vehicle and trainer planes used for piloting practice.
Airframe
During the summer, we decided to purchase a backup airframe, the Believer, which is a surveying and mapping plane that is well suited to our needs. We also began training two new safety pilots since our pilot graduated.
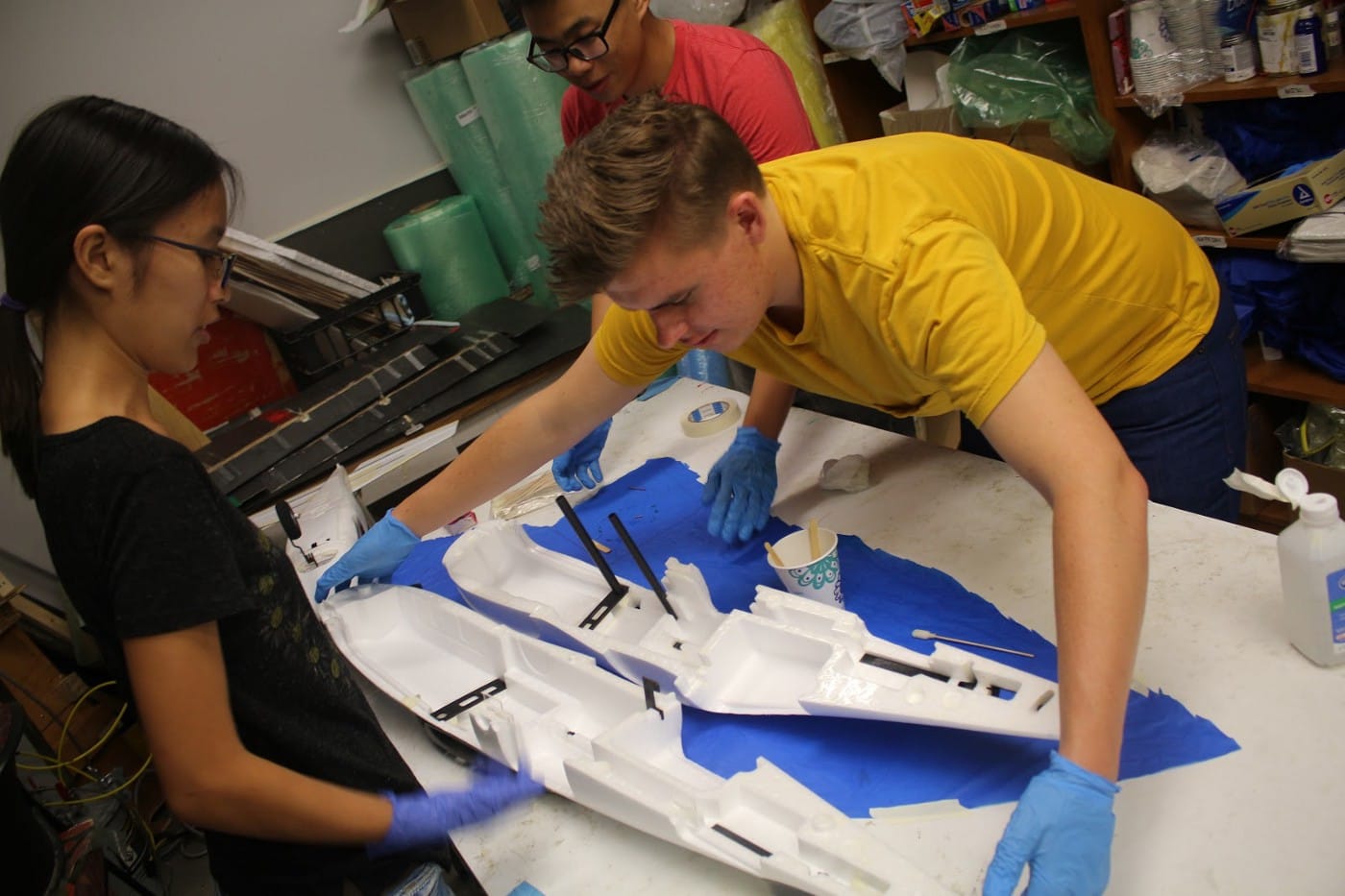
This quarter we have focused on recruiting and onboarding new members. To help with retention we split up our meetings into project meetings for research and design and general meetings for manufacturing. The new meeting structure has been successful in engaging new members. During project meetings, members design an unmanned ground vehicle, research composite manufacturing techniques, and develop improvements to incorporate into our current flight platform. Future projects include a launcher for safer and reliable takeoffs and a new flight platform to accommodate the unmanned ground vehicle, a new component of the competition.
Outreach
Before the start of fall quarter, our team went to the Miramar Air Show. The team had fun at the airshow and enjoyed the team dinner after the event.
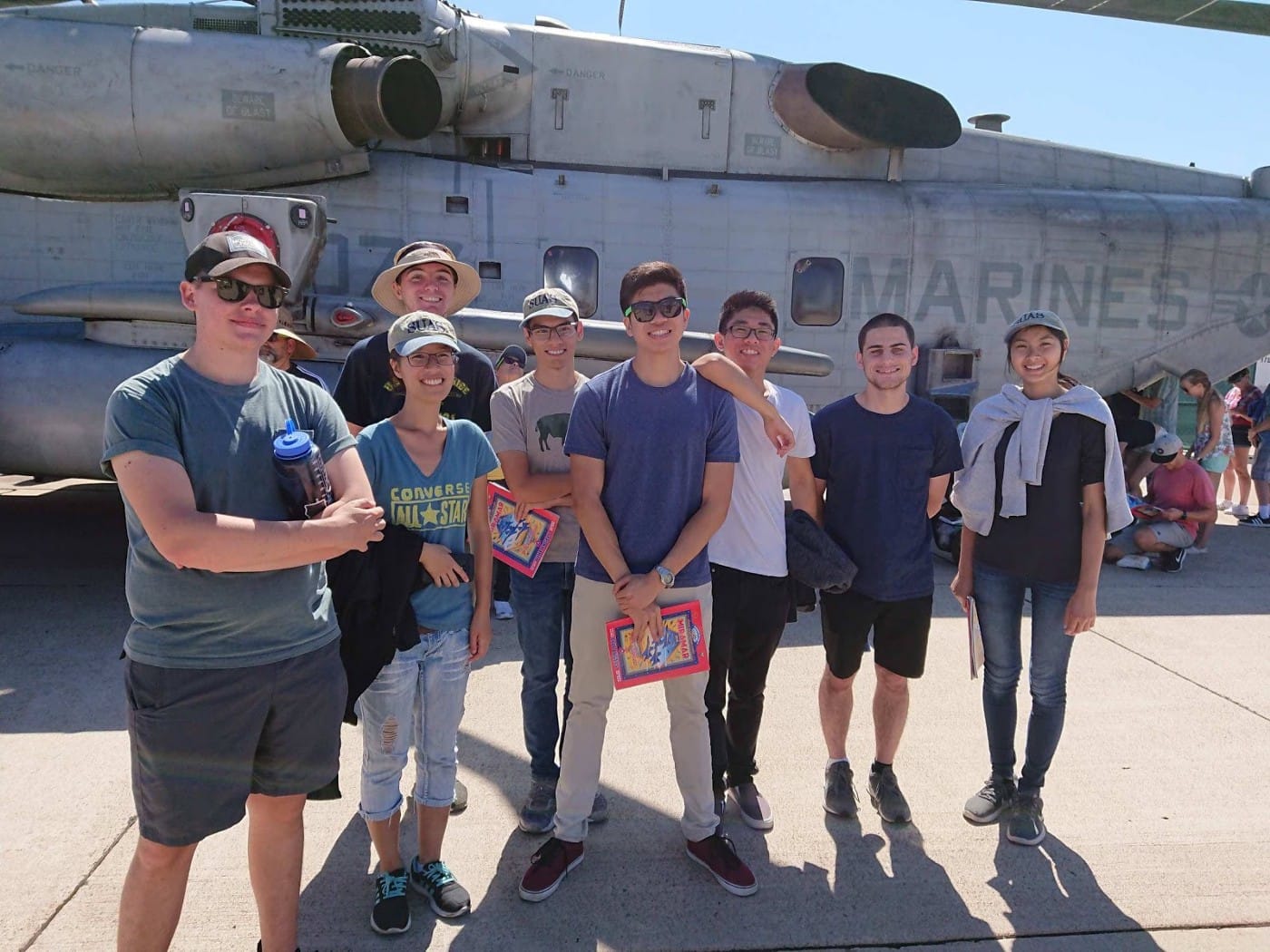
Our team participated in the San Diego Maker Faire, an annual event hosted at Balboa Park, where we interacted with participants and explained what our project team does. We had our 2-axis camera gimbal and a RC plane simulator setup as a interactive exhibit.
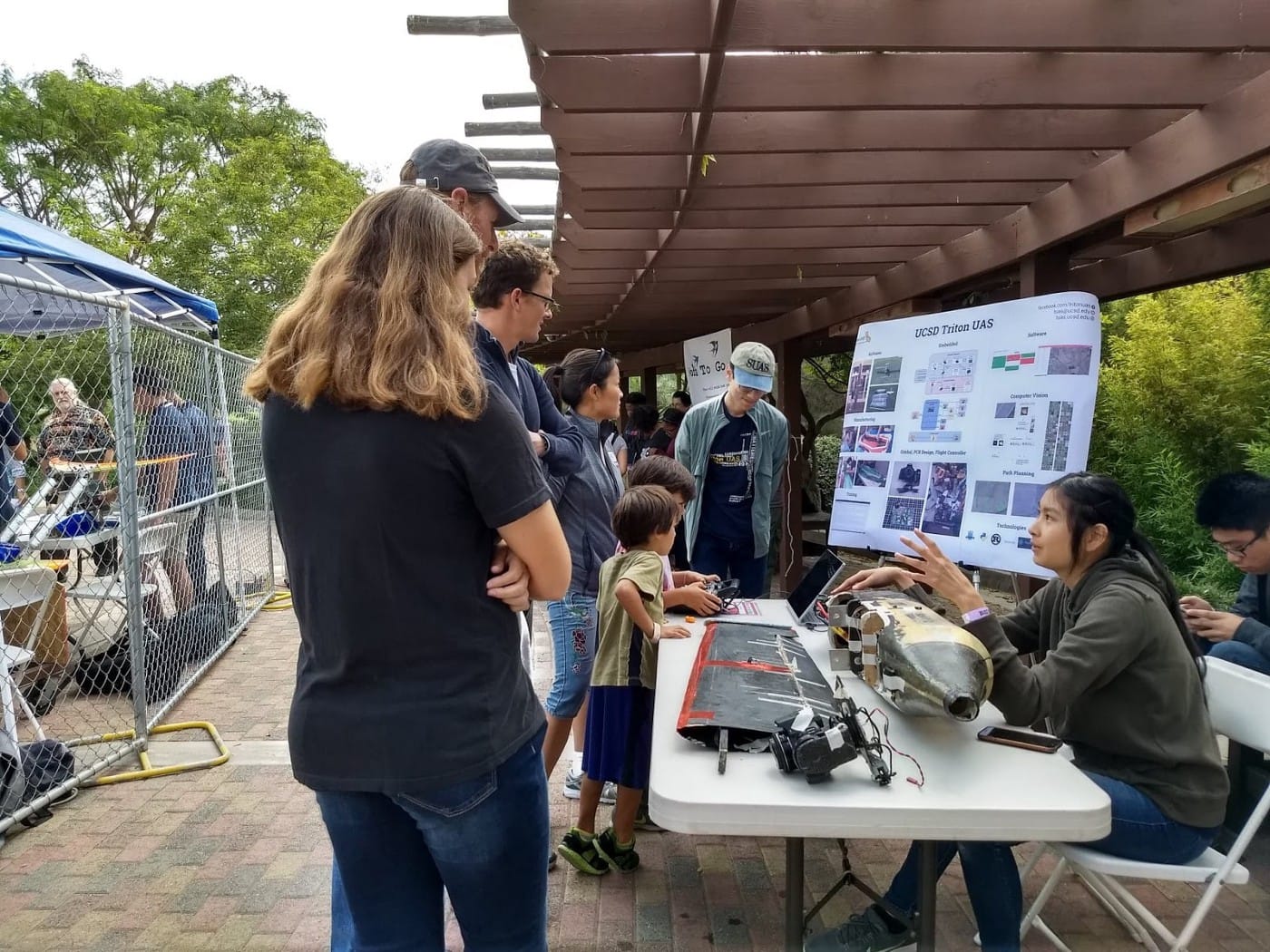
Recruitment at Engineers on the Green, a UCSD engineering student organization recruitment fair, was successful. We recruited around 40 new members.
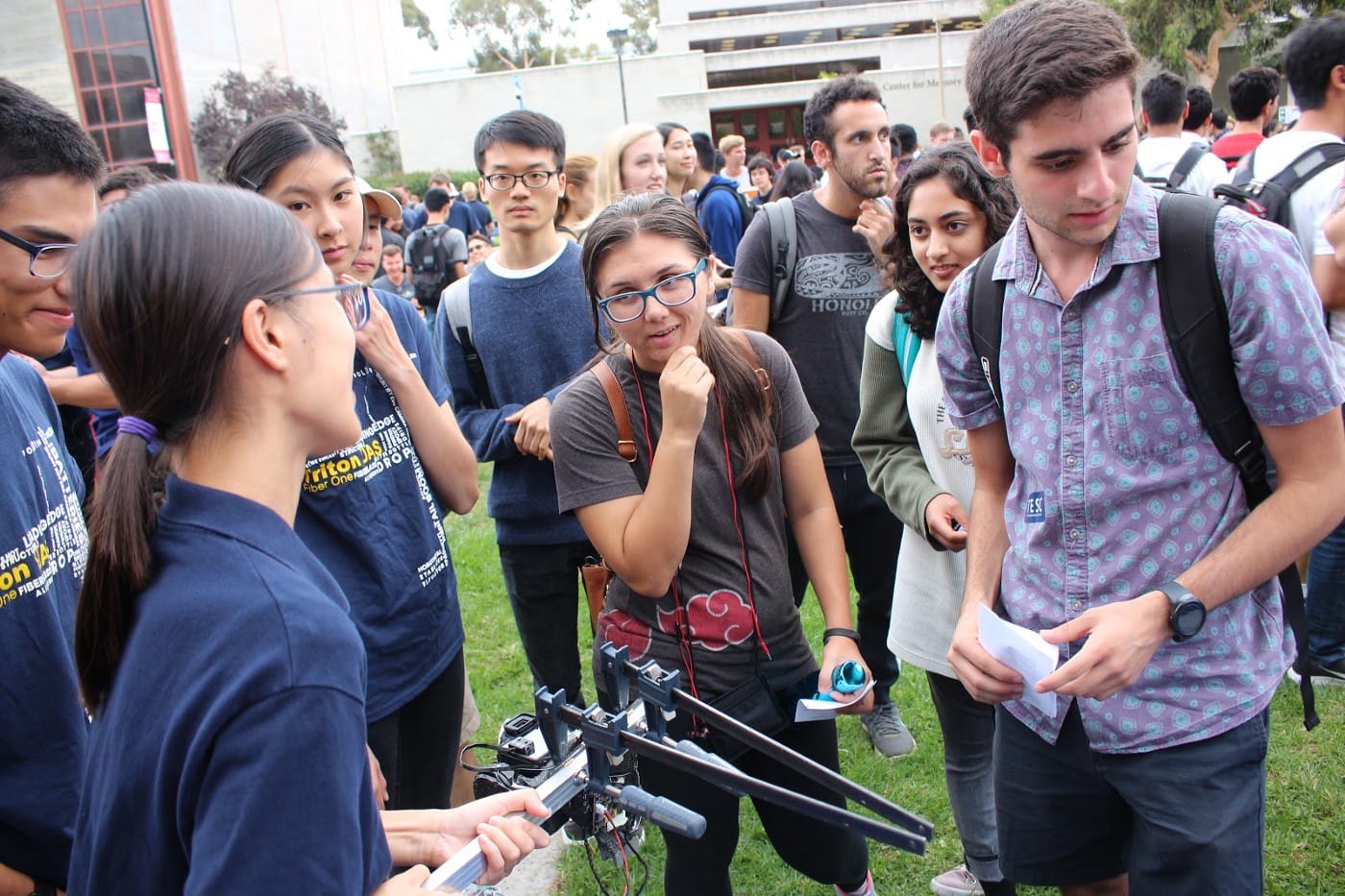
One alumnus advised us to to reach out to other alumni and as a result, we received several generous donations. Applying to on campus funding and reaching out to companies have also proved successful and we have several new sponsors this year including UC San Diego Parents Fund, TESC (Triton Engineering Student Council), Viasat, and Wurzbach Electronics.