The Triton UAS team has accomplished several goals during the 2018–2019 school year. We have made significant progress in refining the structure and algorithms in our software, making it more robust and extensible. Our embedded team has been hard at work adding new features to our electronics to improve the power system and the communication systems. Finally, we have added new features to our flight platform in order to handle both new and old challenges. With these additions and improvements, we are entering the 2019–2020 year prepared and eager to excel at all the challenges of the SUAS competition.
Software Team
The software team improved the autonomy and modularity of our software suite. These improvements are evident in our latest computer vision system. We doubled the accuracy of our character recognition algorithm through transfer learning with ResNet-18 and improved the performance of our segmentation algorithm by adding a Gaussian Blur pre-processing step. We also improved the integration of our software modules so they can make more intelligent decisions. For example, this new integration strategy allows the path planning software to plan to redo mission tasks as the plane executes the mission. To ensure less debugging at test flights, we implemented continuous integration infrastructure to automatically test every code change.
The software team is in a solid position to do well at competition in future years. We currently have software that provides a strong baseline performance on mission tasks. The software goal for next year is to incrementally improve our computer vision and path planning algorithms. This will involve not only implementing better algorithms, but also creating an easy-to-use platform to benchmark said algorithms.
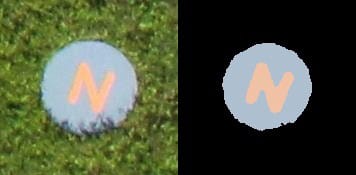
Embedded Team
On the Embedded team, our main focuses were improving our power system and building an antenna tracker to automatically point a directional antenna at our plane during flight. We removed several bugs from our previous power supply board and added more robust connection points to prevent cables from being pulled out over time. We also added a buzzer to automatically alert us when batteries start running low in our plane.
Lastly, we developed our antenna tracker. This automatically points a Ubiquiti Nanostation M, carrier grade equipment designed for long range connection, at our plane during flight. Once this is finished, we will be able to reduce the number of people necessary at test flights and competition by one.
The embedded team intends to refine and improve the payload power system in the plane to allow for better monitoring of the plane status and analysis of the performance of payload components such as the motor or autopilot. In addition, we will be finishing up the antenna tracking system to improve connection quality. We will also be developing a battery discharger to maintain the health of our LiPo batteries.
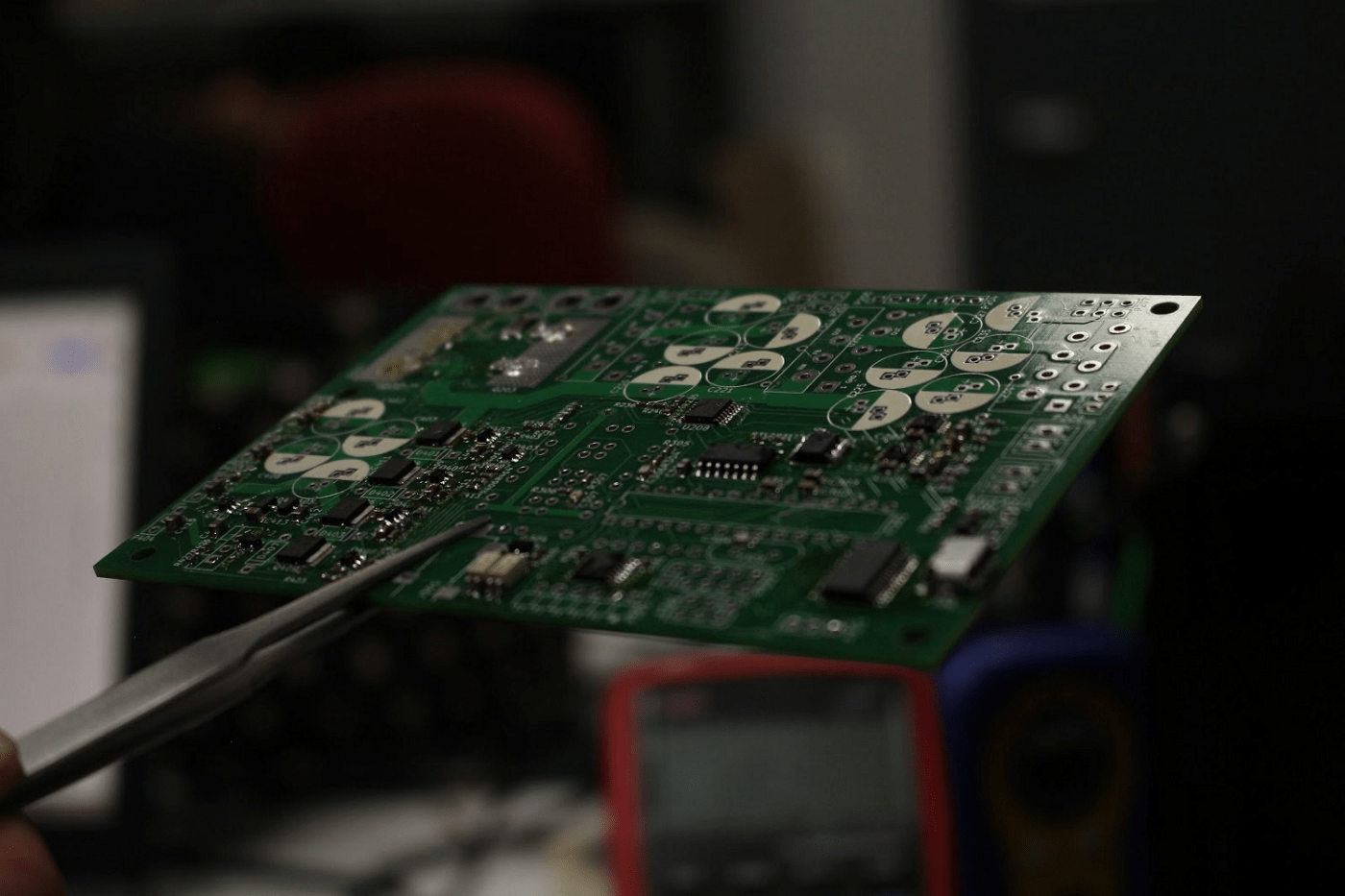
Airframe Team
The airframe team experienced several issues with the current Fiber One aircraft. Our current method of taking off uses a cart, which has proven to be unreliable. Additionally, we noticed damage to the wing spars during less than optimal landings. These challenges led the airframe team to begin design changes and renovations to the Fiber One that include redesigning to include landing gear and redesigning the wing connection. We also prototyped and tested an unmanned ground vehicle using 3D printing to rapidly prototype the body of the vehicle.
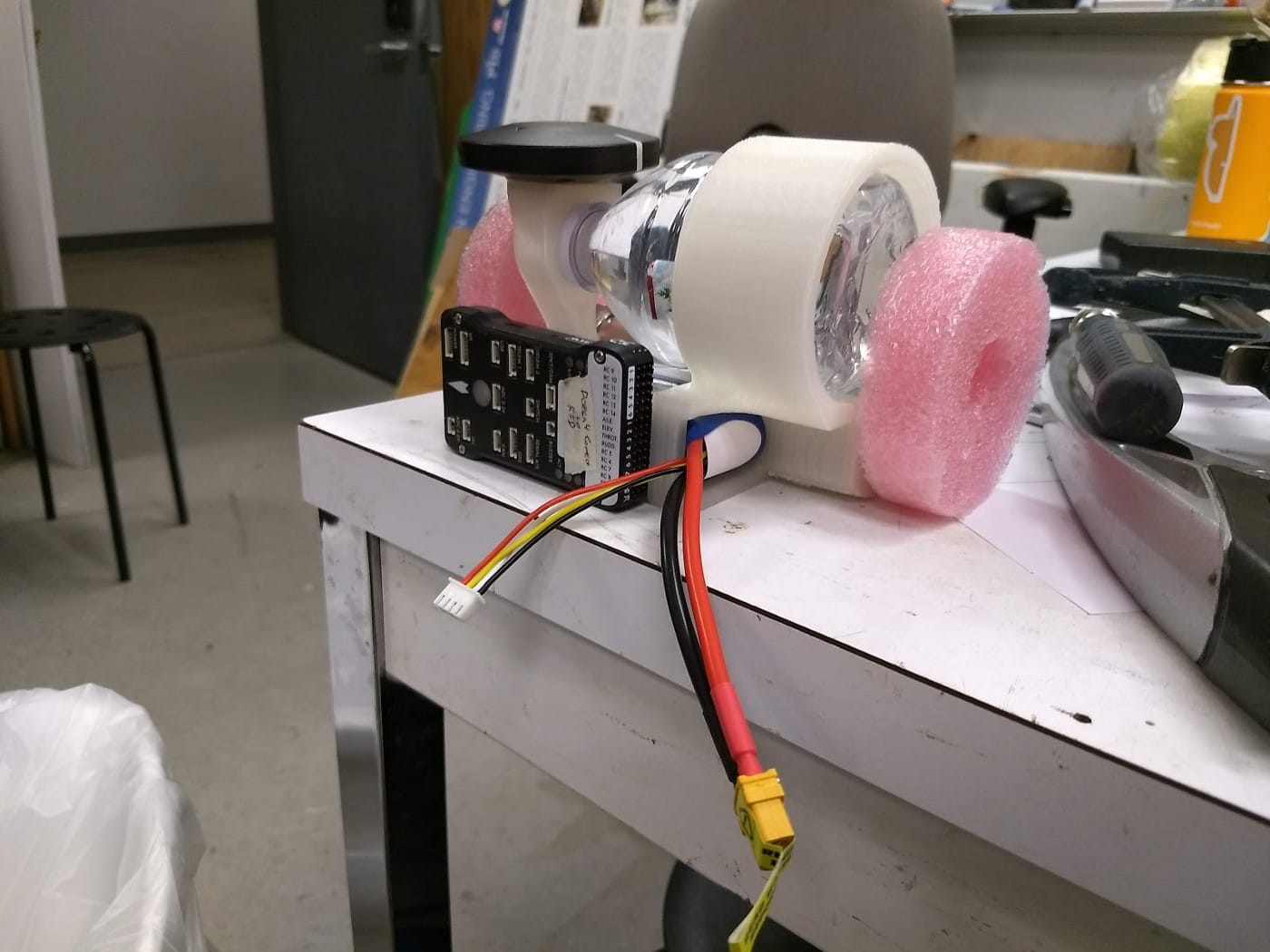
In addition, the team is developing a water bottle drop mechanism in case the unmanned ground vehicle has not undergone adequate testing before competition. A completely new airframe is being designed to better handle the increased payload from the added weight and size of the unmanned ground vehicle and the project is planned to be a two-year endeavour from the design to manufacturing stages.
Test Flights
This year, the team has improved upon organization and communication during test flights. In preparation for test flights, we hold tuning meetings to review what steps need to be taken to PID tune the plane, what maneuvers our plane will perform, and how to analyze our data to discern if a parameter has been successfully tuned. We created test flight roles and assigned a member to every role before each flight to guarantee that all flights would have a sufficient number of people. Additionally, we have designed a number of checklists to ensure test flights are performed safely and consistent.
Further, we plan to increase the use of mock test flights, both to determine whether or not we can make a safe and effective actual test flight, and to allow us to perform system tests and detect many issues which we can repair in the lab without the logistical complexity of a test flight, or even an available airfield.
New Business Team
For this upcoming academic year, we plan to establish a business subteam by reaching out to students from business and management student organizations at the university. This subteam will manage administrative tasks such as interacting with current sponsors, reaching out for companies for new sponsorships, managing our social media pages, and managing club finances. The business subteam will take over these tasks, as we expect them to be better equipped to handle the tasks, and they will enable the other subteam leads to focus on running their own subteam projects. Our new business subteam would be pivotal to advancing the team’s outside connections and procuring the funding necessary to build a high-quality airframe.
Conclusion
In summary, we have improved, and will continue to improve, numerous elements of our aircraft design in all major areas. These improvements will make 2019–2020 our most effective year to date.