Triton UAS is off to a fresh start this year with new members and new leadership. The airframe subteam has worked on and made progress on the unmanned ground vehicle, and rebuilding the main airframe, Fiber One. The embedded team has been hard at work on the antenna tracker as well as the signal and power sister boards. The airframe and embedded team have worked jointly on outfitting and wiring the backup airframe, Swallow, for a maiden flight in the beginning of Winter quarter. The software team worked on generating artificial targets, a user interface for the path planner, and interfacing with the judging server.
General
Despite many core members graduating at the end of last school year (2018–2019), we were successful in recruiting and retaining 28 new members during the annual project team recruitment event, Fall Engineers on the Green. We also have been working on transitioning in new leads as all of the leads from last school year, with the exception of one, graduated. One of the previous software leads, Otto Jursch, is still at UCSD as a master’s student, both embedded leads, Brittany Nguyen and Justin Sun, from last year are now fourth year students at UCSD, and one of the airframe leads, Jessica Chan, has continued on from last year which has eased the process of transitioning in new leads because previous leads are still available to advise new leads and answer questions. Additionally, our safety pilot, Brad Sexton (fourth year student), has been training two new pilots, Hubert Wang (third year) and Shane Vis (second year), to replace Brad as safety pilot once he graduates later this year.
Further administrative changes include the addition of our new business team. The business team will help Triton UAS with administrative tasks such as outreach, sponsorship, and finances to allow other teams to focus on their own goals. Another change that occurred was the adoption of Trello for the entire Triton UAS team. At the suggestion of one of our embedded leads, Emmeryn Gelblicht, the team has started using Trello as an accountability and project management tool for getting tasks done within each subteam. Using Trello has been an invaluable improvement over the previous method of using Google Docs to keep track of tasks. The team plans to contact Trello for a sponsorship to consolidate currently separate Trello boards and expand our use of Trello in the team.
Going forward into the Winter quarter, a maiden flight of our backup airframe, Swallow, is planned for the beginning of Winter quarter. We plan to finish the hardware and electronics setup in the plane and run mock test flights with old leads present so that we have leads with test flight experience guiding the new team. Week 2 is also an opportunity to attract and recruit more members at the Winter Engineers on the Green. The subteams will also continue training their current members and any new members that are recruited this quarter. An important goal moving forward is to dedicate extra effort in documenting each subteam’s work to serve as a detailed reference for future members.
Airframe Team
The main focus for the airframe team this quarter was recruitment and retention. With the exception of our two leads, the entire rest of our airframe team either graduated or were not retained. This year, we were able to recruit and retain seven members so far, a much higher number than we had at this point last year. Much of the quarter was spent training our new members with events such as our Solidworks Crash Course, our Intro to Composite Layup Workshops, as well as through continual guidance and training from our leads during airframe meetings.
The airframe team has also been focusing on getting our backup airframe, the Swallow, ready for its maiden flight. This quarter, the team used MotoCalc to pick the optimal power system: propellor, brushless motor, electronic speed control (ESC), and batteries. Additionally, using Solidworks, we designed and printed servo cases to properly house the selected servos and a new gimbal mount that allows our current gimbal design for the Fiber One, our primary airframe, to be mounted in the Swallow. We also determined the location of all the electronics, based on easy access during troubleshooting, ease of wire management, and the location of the center of gravity.
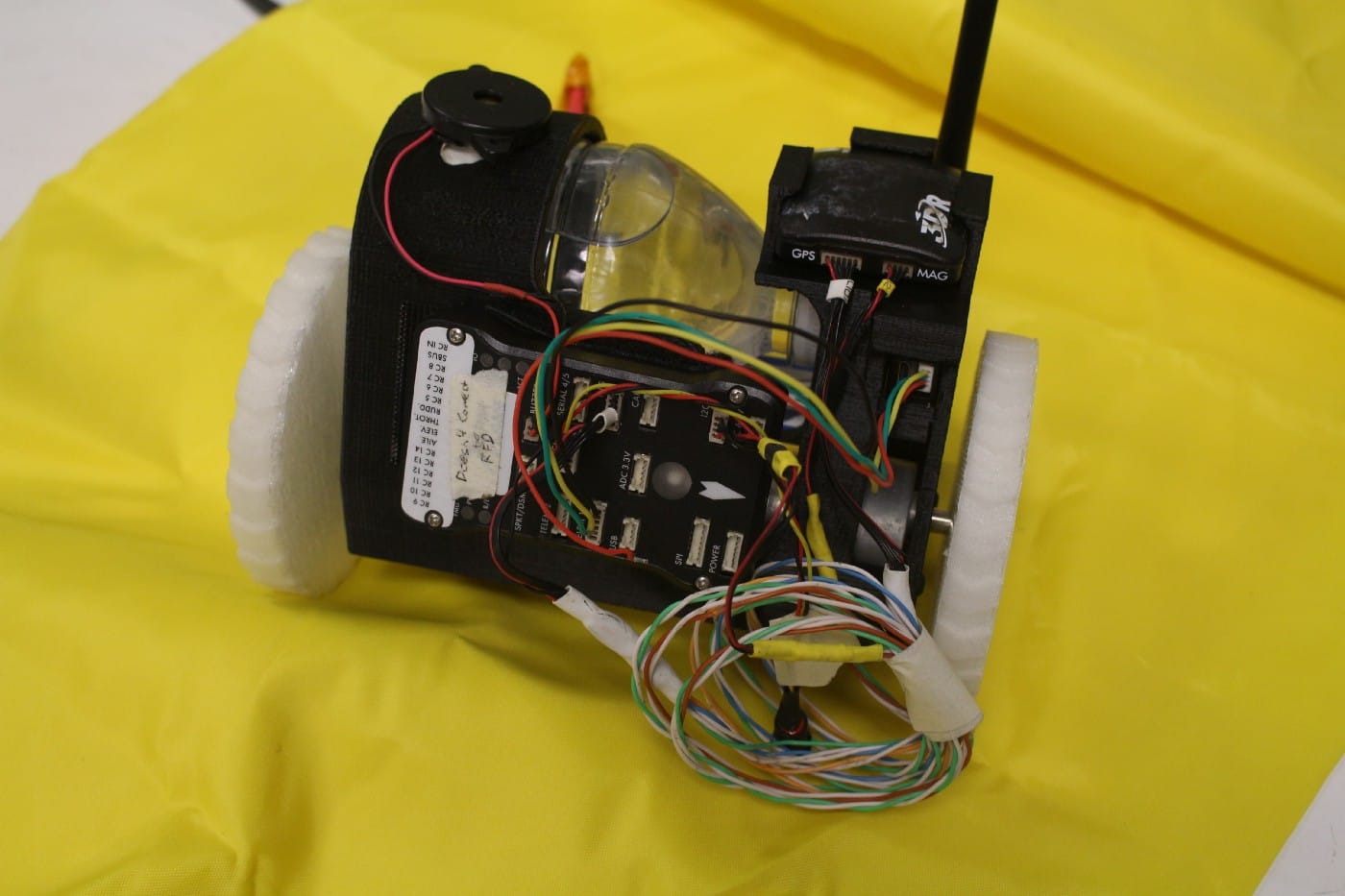
A few members within our airframe team have been working on improving last year’s prototype of the unmanned ground vehicle (UGV). One crucial improvement was decreasing the size and weight of the electronics. When we looked into optimizing the size of our electronics, we found that we could use a smaller radio, GPS, and a much smaller battery. Knowing exactly what electronics we were using allowed us to add custom secure mounting for all the necessary electronics. We also performed some preliminary testing to check that the UGV is capable of driving, 3D printed several different designs for a new set of wheels, and started optimizing the chassis by removing unnecessary material and weight.
Lastly, our airframe team has started making efforts toward rebuilding our primary platform, the Fiber One. So far, the preparation has almost been completed for manufacturing all four parts of the outer wing skins. Additionally, we have tested a possible new manufacturing method for the tail boom.
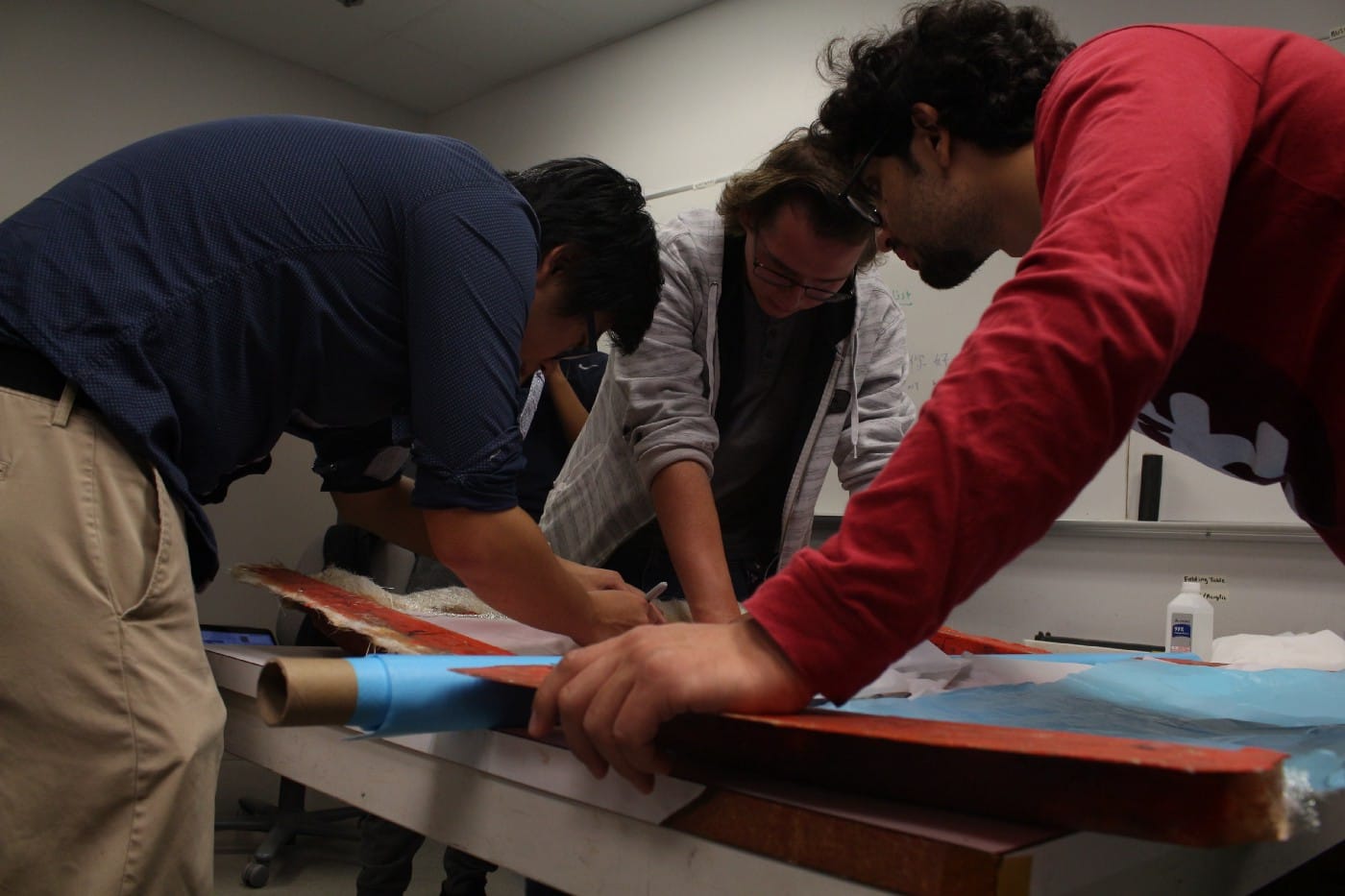
The airframe team’s goals for next quarter span across all the same areas of focus as our progress from this quarter.
For the Swallow, as stated above, we are planning on having our maiden flight during the beginning of winter quarter, so we are aiming to have the Swallow ready for flight by that time. For the airframe team, this would include mounting the pitot tube, designing and manufacturing a motor mount, and mounting all electronics.
Concerning the UGV, we are looking to have the UGV completed and ready for full mission testing by the end of the quarter. This would entail finalizing the design, testing the release mechanism, calibrating the electronics, and conducting drive tests and drop tests with the UGV.
Our goal this quarter for the Fiber One, is to finish all manufacturing by the end of the quarter. Finishing by the end of the quarter would allow us to test fly at the beginning of the Spring quarter so that we could compete with our primary airframe.
Embedded Team
Our embedded team this quarter consisted of three retained members, who have been hard at work resulting in strong progress on four different projects.
For the antenna tracker, the team worked on brainstorming and designing a virtual prototype of the software that will power the tracker. This required us to familiarize ourselves with the protocols pertaining to the communication between the antenna tracker controller and the ground control station. Alongside these tasks, we have also been conducting research for the appropriate mathematical models to implement for the software.
We have also made developments on the power distribution board with making the decision to split the power distribution board (PDB) into two boards, power and signals, to mitigate any possible contingencies that we could encounter in the process of design, building, and in-flight. By having two boards we aim to reduce the effect of either board failing, and each board will be less populated with components, making the building process less prone to mistakes. Additionally, we also opted to add more telemetry data outputs to the signals and power boards. Specifically, there will be an added Coulomb counter to log battery usage for both the motor and the payload, and we will measure the voltage of each cell from the onboard battery to ensure that they are balanced.
The power board will use different components, as there are no exact through-hole corresponding components for the devices that previous PDB used. However, the power board will have the power lines that the PDB outputted, since the plane will use most of all of the on-board electronic devices that it had last year. At the moment, the power board is still at component selection stage as we want to ensure that there are not any critical failures on our power lines.
The team has entered early prototyping for the signals board, with a preliminary high-level design centered around the highly standardized and easily expanded i2c bus. Problems may occur with devices at different logic voltages; however, this can most likely be accounted for by using transistors as a simple voltage converter, which is far more simple than the complex topology necessary for UART (universal asynchronous receiver/transmitter). The i2c bus can be connected to many devices sharing a common pair of signal wires, including a Raspberry Pi (for testing), Jetson TX2 with Orbitty carrier, Pixhawk 2, and many microcontrollers (including Arduino), allowing for design flexibility, compatibility, and expandability. Other signals can be supported simply by configuring an Arduino or similar device supporting the necessary protocol to communicate over i2c; such support for UART,used by the radio transceiver and our current OBC (on board computer) system, is currently under development.
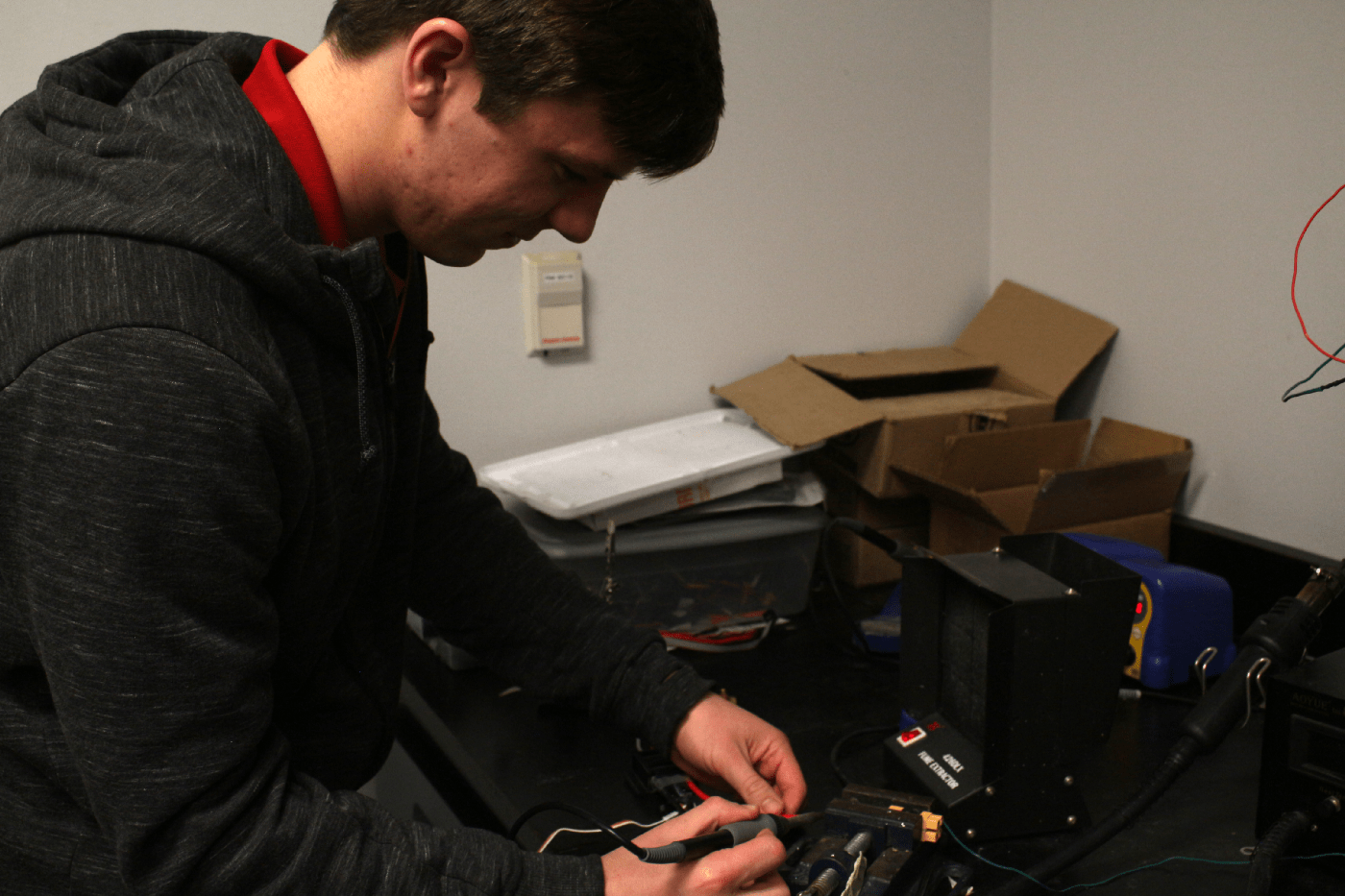
For the upcoming quarter, the embedded team aims to finish wiring the plane for all of the onboard devices and complete all the necessary PID tuning for the plane. Additionally, we intend to have working prototypes for both the signals and power boards to use during the upcoming test flights later in the quarter. For this, we will need to build a proof of concept for both boards during the early stages of the Winter quarter and construct board designs that fit in our plane. Finally, we plan for the antenna tracker to have working software to test at the end of the quarter.
Software Team
During the Fall quarter, the software team made significant progress in both the development of the software suite and the recruitment of dedicated team members. Comprised of ten active members, each software subteam (computer vision, infrastructure, and path planning) have at least two members allocated to them. This division of labor allows for each member to become especially skilled at their software element, which will aid in the problem of knowledge transfer going into the future years of Triton UAS. Having specialized experts will allow future new members to learn skills more efficiently and broaden the capabilities of the software team as a whole.
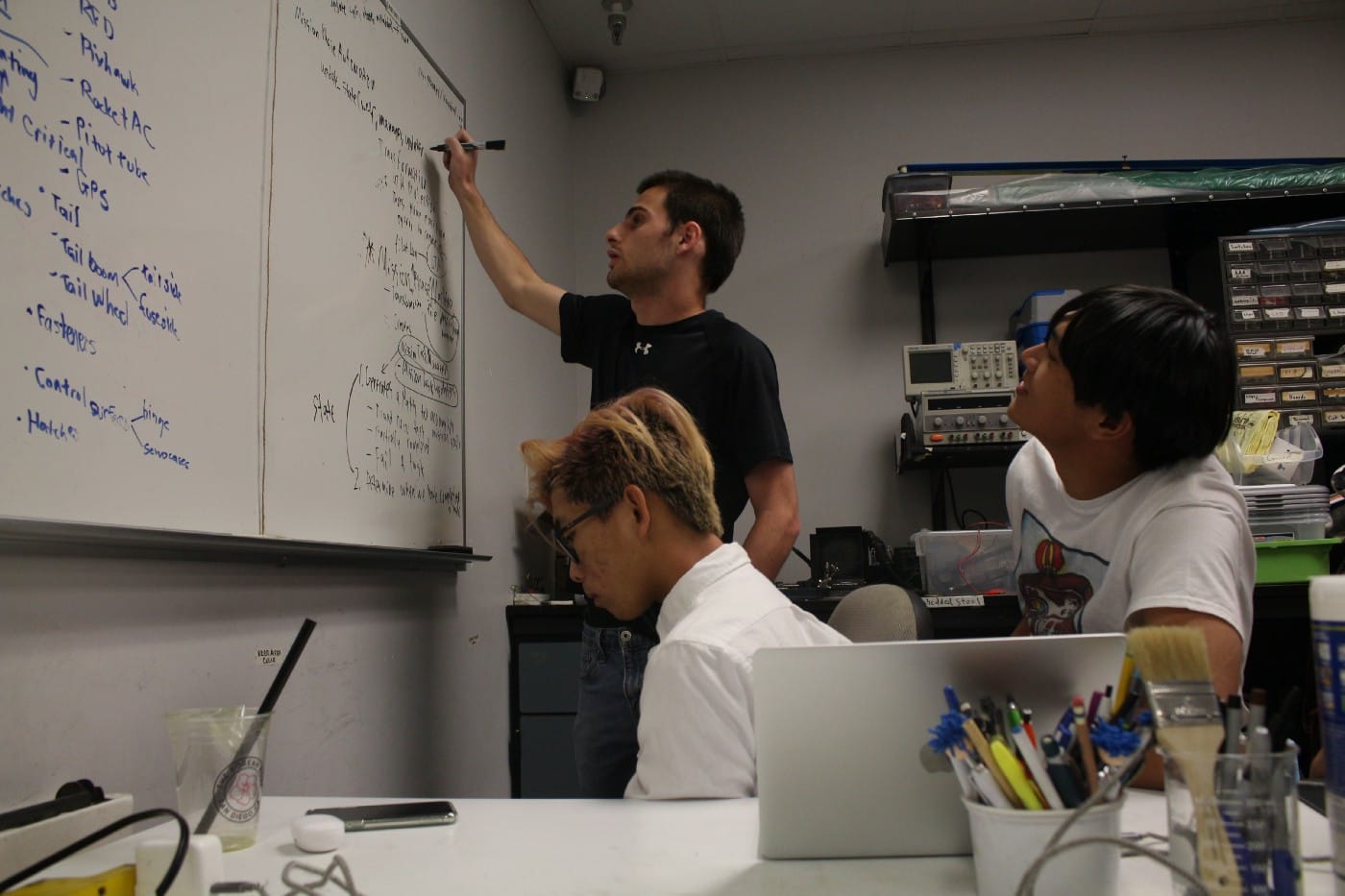
As many newcomers in the team were interested in computer vision despite having little experience, much of this quarter was invested in teaching our new members to use Python, OpenCV, and Pytorch; furthermore, the new members were also taught how to use computer vision techniques including K-NN and concave hull for segmentation.
In the computer vision team, we have improved and tailored an open source tool to generate artificial targets, for future use in training machine learning models for color, shape, and character classification. This tool has been modified to generate the binary mask and contours of the targets (i.e. the outline of the shape/character of the target), which will be useful as labels/ground truth to train on. Additionally, a user interface has been created for the path planner. Previously, the path planner would only output numerical values for waypoints, which is difficult to visualize or present to interested members. This has now been replaced by a Python GUI.
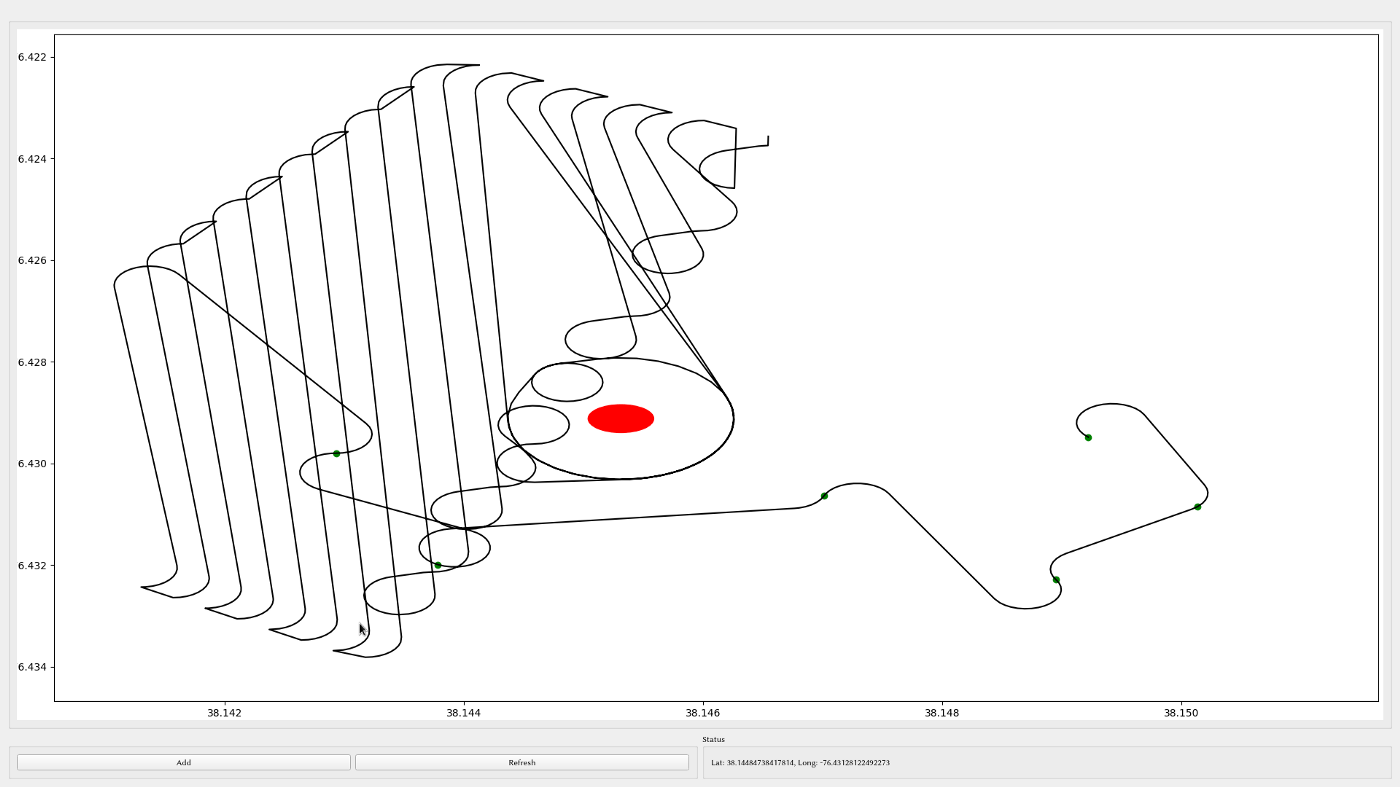
The infrastructure team has been working on interfacing with the judging server, with the team completed in compiling new protobufs into Golang and Python. In addition, members who are interested in infrastructure are hard at work learning Golang and documenting the API endpoints for our Hub.
The software team’s goals for the Winter quarter are to finish all the components of the software suite in order to complete mission testing. This includes testing different turn radii to determine the optimal speed to performance. Specifically, the computer vision (CV) infrastructure needs to be completed and the individual components (saliency, segmentation, and classification) need to be integrated into the system. The CV suite uses a master-agent design pattern in order to perform the multiple transformations concurrently, thus requiring more test targets to be created in order to more effectively benchmark the classifications using our different neural networks.
In regards to the planning suite, the Dubins curve algorithm is planned to be completed and integrated with our ground control station. Generation of the waypoint path is done using Rust; however, it needs to be improved to create a flight plan that can cater to the design constraints of our UAV. In addition, the team intends to improve upon our obstacle avoidance. Dynamic obstacle avoidance and path modification is necessary in order to avoid moving obstacles during the SUAS competition, which will be a different team’s plane that is flying at the same time as ours.
Both path planning and CV are arranged to be integrated with the AUVSI interoperability system to emulate the competition mission environment.
For the Hub, all methods of communication should be standardized. More specifically, the intent is to take all the different networking protocols, including REST, GRPC, MavLink, ZMQ, etc. and consolidate them into one standardized protocol (ideally ZMQ + Protobuf). Lastly, the team plans to document all the endpoints and structure of data being sent around.
Conclusion
Heading into the upcoming Winter Quarter, Triton UAS and our subteams are actively working to bring our project together ahead of the SUAS 2020 competition. Our airframe team plans to finish the manufacturing process of our main airframe, the Fiber One, with the intention of holding Fiber One test flights at the beginning of Spring Quarter. Our embedded team is completing the work required for all the onboard electronics and PID tuning for our airframe, along with completing prototypes of the signals and power boards. The software team aims to finish up the necessary components for the software suite in relation to mission testing and computer vision infrastructure.